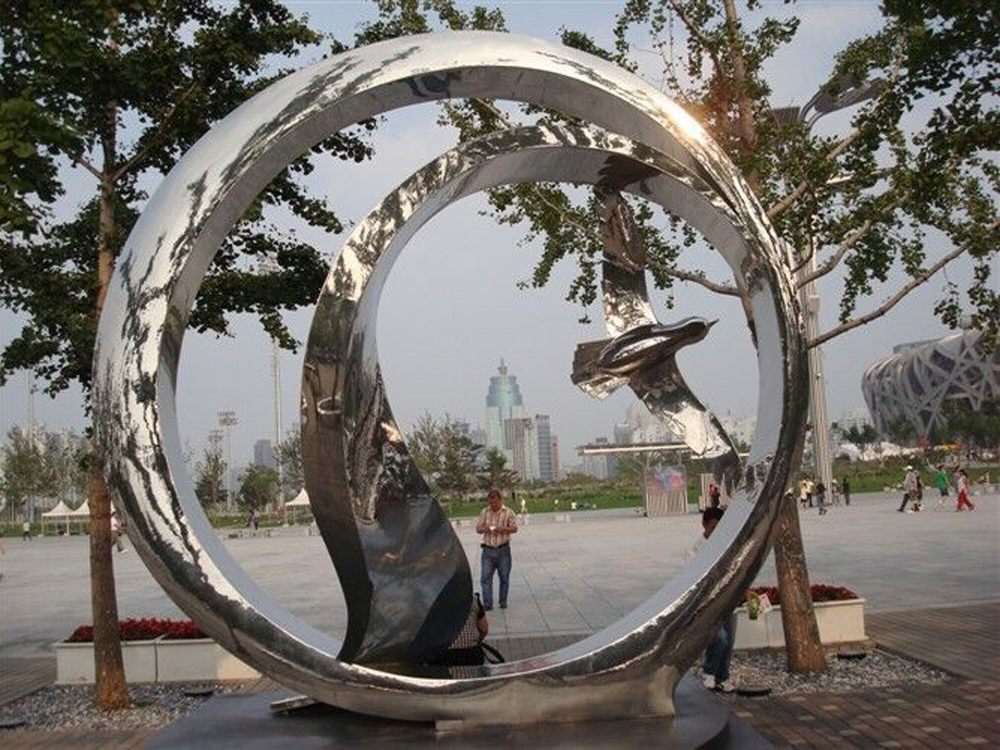
Creating durable and aesthetically pleasing pottery requires meticulous attention to the drying and firing processes. Artisans employ a variety of techniques to prevent cracking and warping, ensuring their pieces remain intact and visually stunning.
1. Slow and Even Drying: Rapid drying is a common cause of cracks. Artisans often cover their pieces with plastic or damp cloths to slow moisture evaporation, allowing the clay to dry uniformly.
2. Proper Wedging and Kneading: Air pockets in the clay can lead to cracks during firing. Thorough wedging removes these pockets, creating a consistent texture that withstands heat stress.
3. Controlled Kiln Firing: Gradual temperature increases in the kiln prevent thermal shock. Artisans use a slow ramp-up and cooling cycle to minimize stress on the clay structure.
4. Use of Grog or Sand: Adding grog (pre-fired clay) or sand to the clay body improves its thermal stability, reducing the risk of warping during firing.
5. Even Thickness: Uneven clay walls can dry and fire unevenly, leading to warping. Artisans ensure uniform thickness throughout the piece for balanced drying and heating.
By mastering these techniques, artisans produce high-quality pottery free from cracks and warping, showcasing both skill and precision in their craft.