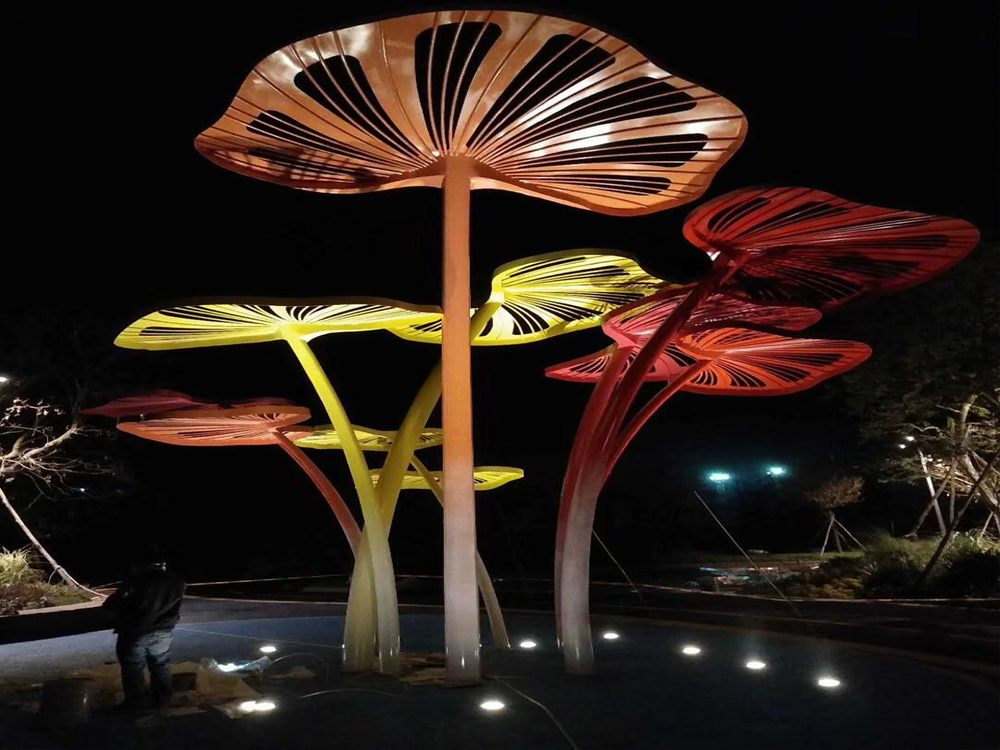
Creating porcelain sculptures with organic shapes presents unique challenges for artists and manufacturers alike. The delicate nature of porcelain, combined with the complexity of mimicking natural forms, requires a blend of technical skill and artistic vision.
One key approach is the use of advanced molding techniques. Many artists employ slip casting with custom-made plaster molds to capture intricate organic details. Others prefer hand-building methods like coiling or pinching, which allow for greater spontaneity in shaping. Manufacturers often combine these techniques with 3D printing for precise replication of complex designs.
Firing presents another significant hurdle. Organic shapes are more prone to warping or cracking during the kiln process. Artists address this by carefully controlling drying times and using specialized kiln furniture for support. Some incorporate grog (pre-fired clay particles) into their porcelain mix to improve structural stability.
Surface treatment requires particular attention when working with flowing, natural forms. Many artists develop specialized glazing techniques to enhance the sculpture's organic qualities, such as layering translucent glazes to create depth or using oxide washes to accentuate textures.
Contemporary solutions include the development of more flexible porcelain formulations and the integration of digital tools in the design phase. These innovations allow for greater experimentation while maintaining the material's signature delicate appearance.
Ultimately, successful organic porcelain sculptures result from a deep understanding of both the material's limitations and the creative possibilities it offers, demonstrating how technical mastery and artistic expression can work in harmony.