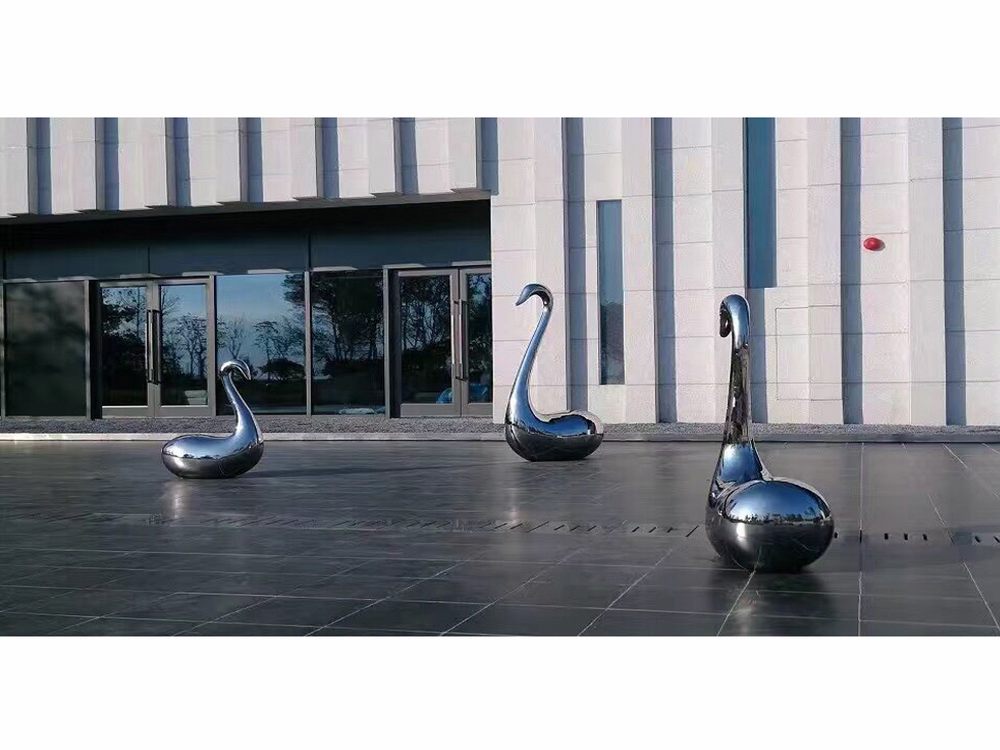
Creating porcelain sculptures with delicate appendages is a meticulous art form that demands precision, patience, and innovation. Artists and manufacturers face numerous challenges, such as structural fragility, uneven drying, and firing risks. To address these, they employ specialized techniques like slip casting for uniformity, reinforced armatures for stability, and controlled drying to prevent cracks.
Advanced kiln technologies ensure even heat distribution, reducing warping during firing. Additionally, artists often hand-sculpt intricate details separately, attaching them with slip—a liquid clay mixture—before firing. This method minimizes breakage while preserving aesthetic integrity.
Manufacturers also experiment with hybrid materials, blending porcelain with polymers for enhanced durability without compromising elegance. Collaboration between artists and engineers has led to breakthroughs in 3D printing, enabling precise replication of fragile designs.
Ultimately, the fusion of traditional craftsmanship and modern technology allows these delicate masterpieces to endure, captivating audiences with their ethereal beauty.