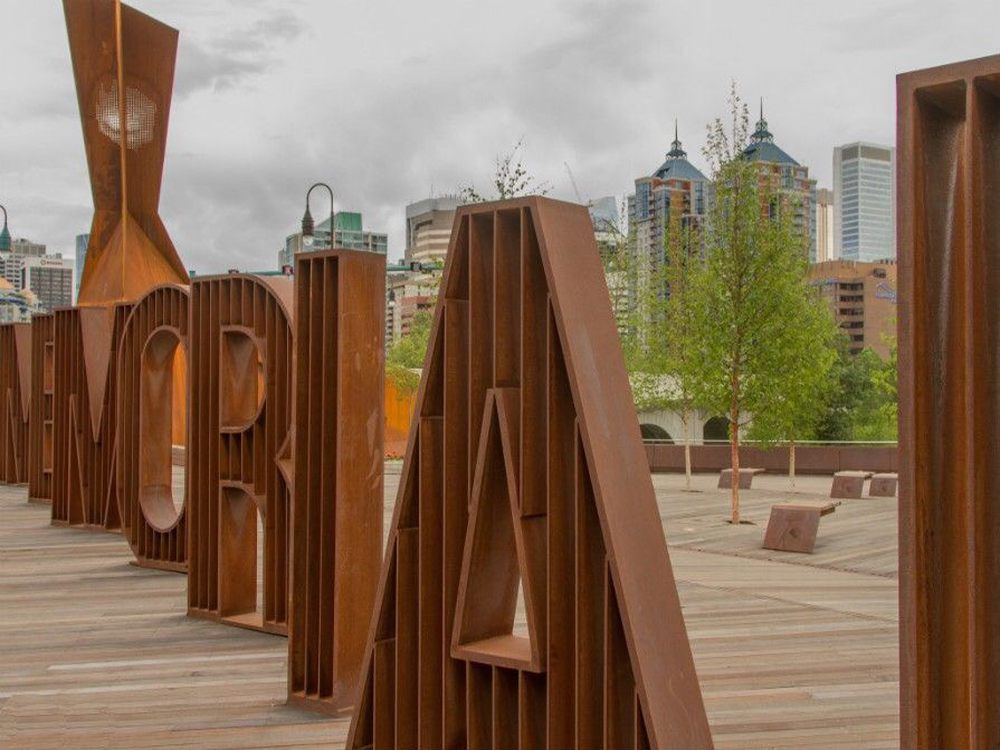
Porcelain sculptures are admired for their delicate beauty, but their fragility under sudden temperature changes poses a significant challenge. Artists employ several strategies to enhance thermal shock resistance, ensuring longevity and durability in their creations.
1. Clay Body Composition: Selecting the right clay mixture is crucial. Many artists incorporate materials like grog (pre-fired clay particles) or chamotte to reduce shrinkage and improve thermal stability. High-quality kaolin with balanced silica and alumina content also minimizes cracking.
2. Controlled Firing Process: Gradual heating and cooling in the kiln prevent rapid expansion or contraction. Artists often use slow bisque firing and multiple glaze firings at carefully calibrated temperatures to strengthen the sculpture’s structure.
3. Glaze Engineering: Specialized glazes with low thermal expansion coefficients are applied to match the clay body’s properties. Layering compatible glazes or using crack-resistant formulations helps absorb stress caused by temperature fluctuations.
4. Design Adaptations: Sculptors avoid sharp edges or thick-to-thin transitions, which are prone to cracking. Hollow constructions and even wall thickness distribute heat more evenly during firing and usage.
5. Post-Firing Treatments: Some artists anneal finished pieces or apply protective coatings to further mitigate thermal stress.
By combining these techniques, ceramic artists create porcelain sculptures that withstand thermal shock while maintaining artistic integrity. Innovations in materials and firing technology continue to push the boundaries of what’s possible in this delicate medium.