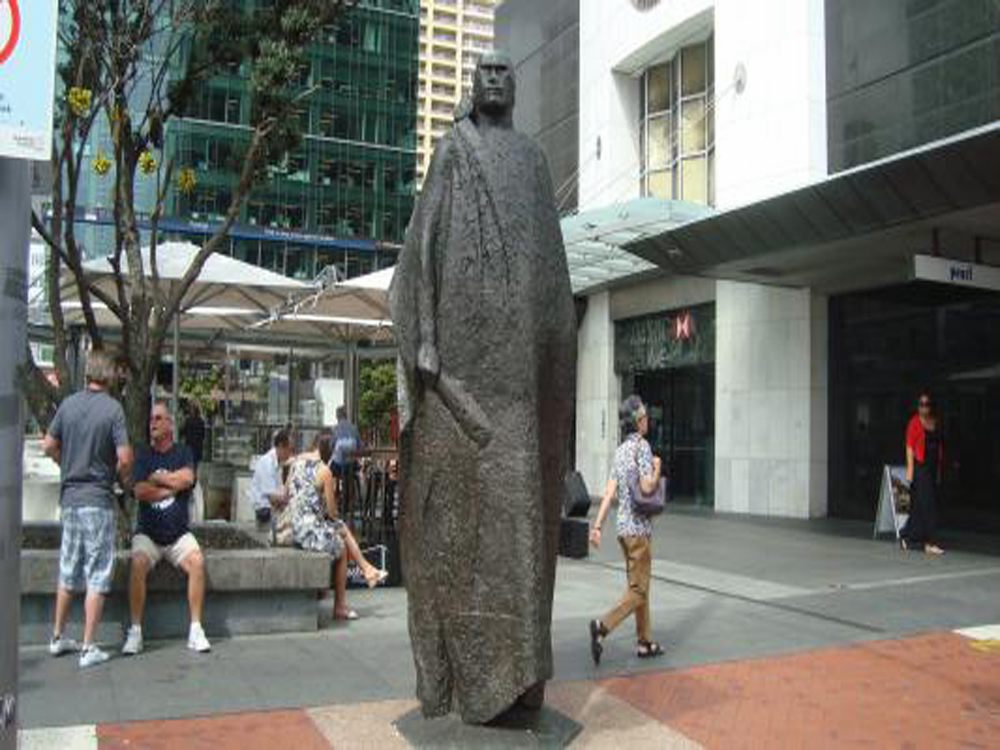
The creation of porcelain sculptures has entered a revolutionary phase where age-old ceramic techniques intersect with advanced technology. Contemporary artists now employ tools like 3D modeling software and digital fabrication to push the boundaries of this delicate medium.
Modern porcelain artists begin their process with digital sculpting programs such as ZBrush or Blender, allowing for precise manipulation of complex forms that would be nearly impossible to achieve by hand. These digital designs then transition to physical creation through either CNC milling of clay or direct 3D printing using specialized ceramic pastes.
The technological integration extends beyond shaping. Artists utilize computational design to create intricate lattice structures that maintain strength while reducing material weight. Some incorporate augmented reality during the glazing process, projecting color patterns onto unfired pieces for precise application guidance.
Traditional skills remain vital - artists must understand clay behavior, firing temperatures, and glaze chemistry. The fusion comes in combining this knowledge with tech like kiln controllers that precisely monitor firing curves or AI algorithms that predict structural stress points in designs.
This synergy produces astonishing results: porcelain pieces with impossible thinness, dynamic kinetic elements, or embedded digital components. The marriage of craft and computation is redefining what's possible in ceramic art, creating works that honor tradition while embracing the future.