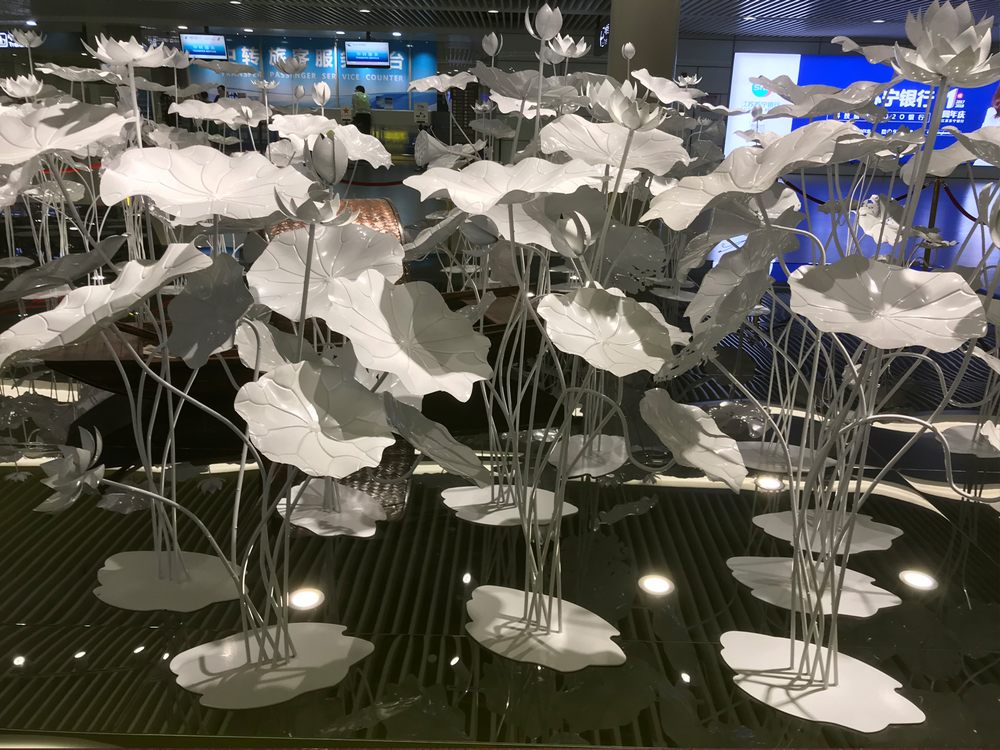
Maintaining consistent color pigmentation across batches of porcelain sculptures presents several complex challenges that require meticulous attention throughout the production process. The primary difficulty stems from the inherent variability of ceramic materials, where even slight differences in clay composition or mineral content can significantly alter final colors. Glaze formulation presents another critical challenge, as precise chemical balances must be maintained batch-to-batch to achieve identical hues.
Firing conditions create substantial variability, with temperature fluctuations of just a few degrees potentially changing color outcomes dramatically. The oxidation/reduction atmosphere within kilns proves particularly difficult to control consistently across multiple firings. Additionally, pigment particle size distribution affects color saturation and must be carefully monitored.
Production timing introduces further complications, as extended storage periods between batches may lead to material settling or moisture absorption that alters application properties. The human factor in manual glaze application also contributes to inconsistencies, where brushstroke variations can create noticeable differences in finished pieces.
Advanced solutions include computerized color matching systems, standardized material sourcing protocols, and precisely controlled kiln environments. Many studios now implement digital spectrophotometers to quantify color differences and adjust formulations accordingly. Despite these technological aids, achieving perfect batch-to-batch color consistency remains one of the most demanding aspects of porcelain sculpture production, requiring constant vigilance at every manufacturing stage.