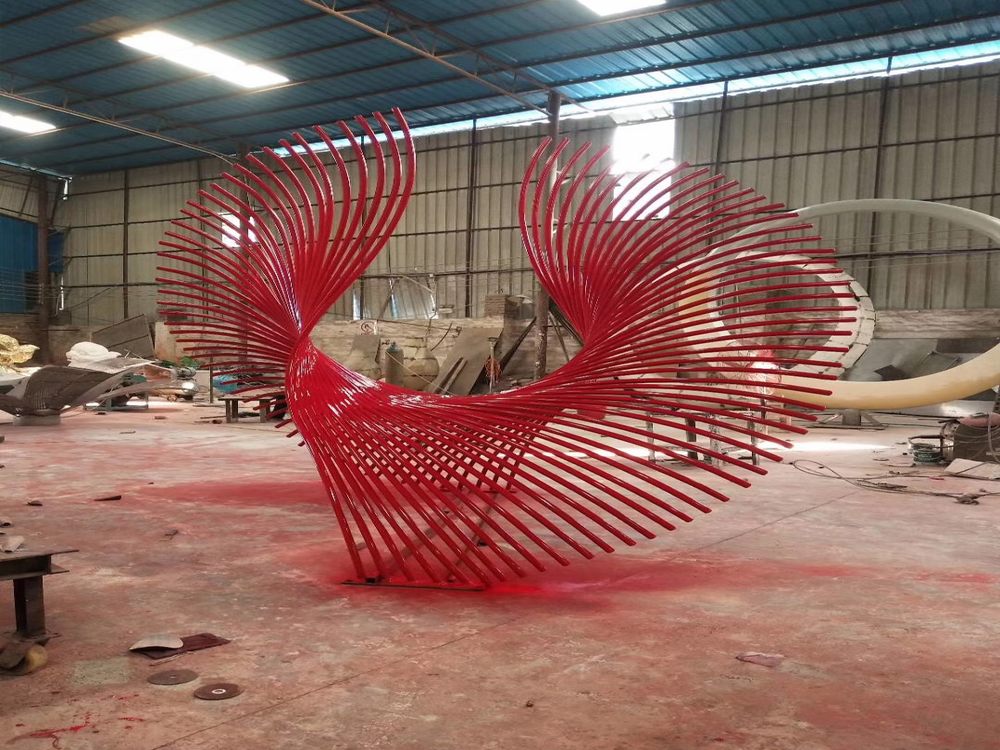
Achieving consistent color matching in hand-painted porcelain sculptures is a meticulous art form that combines tradition, chemistry, and precision. Master artisans rely on three core techniques: First, they create custom pigment recipes by grinding and blending mineral-based colors to exact ratios, often passed down through generations. These formulas account for how hues transform during kiln firing. Second, artists maintain strict control over brushwork pressure and layering – thinner coats produce lighter tones while thicker applications deepen colors. Third, craftsmen use standardized lighting conditions in their studios to evaluate shades, as natural and artificial light can dramatically alter color perception.
The process begins with test tiles, where pigments are trialed at different firing temperatures to predict final results. Experienced painters mix large batches of each color at once to ensure uniformity across multiple pieces. They also employ a "wet-on-wet" technique for seamless gradients, keeping edges moist to prevent visible brush strokes. Modern artisans sometimes supplement traditional methods with digital color meters to verify consistency, though most still prefer trained human eyes capable of detecting subtle variations invisible to machines.
Temperature plays a crucial role – even a 10°C variation in the kiln can shift colors. Veteran craftsmen maintain detailed firing logs tracking how specific pigments react to different heat profiles. This empirical knowledge allows them to compensate for environmental factors like humidity that affect paint viscosity and absorption. The result is breathtaking color continuity across porcelain collections, where each handcrafted piece appears perfectly matched despite being individually painted.