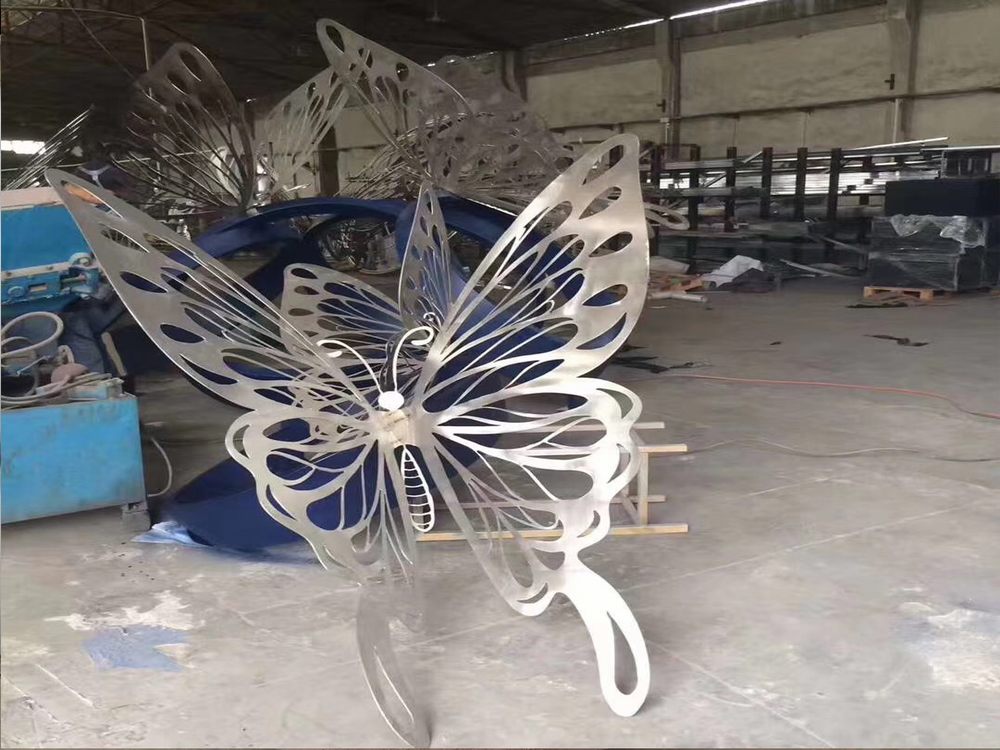
Creating porcelain sculptures with delicate, protruding parts is a demanding art form that requires precision and expertise. One of the most common challenges is structural fragility. Thin or extended sections are prone to cracking or breaking during shaping, drying, or firing. Artists must carefully balance moisture content and support these vulnerable areas with temporary armatures.
Another issue is uneven drying rates. Protruding elements dry faster than thicker sections, leading to warping or stress fractures. Slow, controlled drying in humidity-controlled environments is essential. Kiln firing presents further risks—thermal shock can cause cracks, while gravity may distort unsupported protrusions. Sagging or slumping is a frequent problem, requiring precise kiln shelf placement or custom stilts.
Glazing delicate parts also poses difficulties. Heavy glaze application can weigh down thin extensions, while uneven coverage may create weak points. Many artists use spray glazing or multiple thin layers to mitigate this. Finally, transporting and displaying such sculptures demands specialized packaging and mounts to prevent damage. Mastering these challenges separates amateur attempts from professional-quality porcelain art.