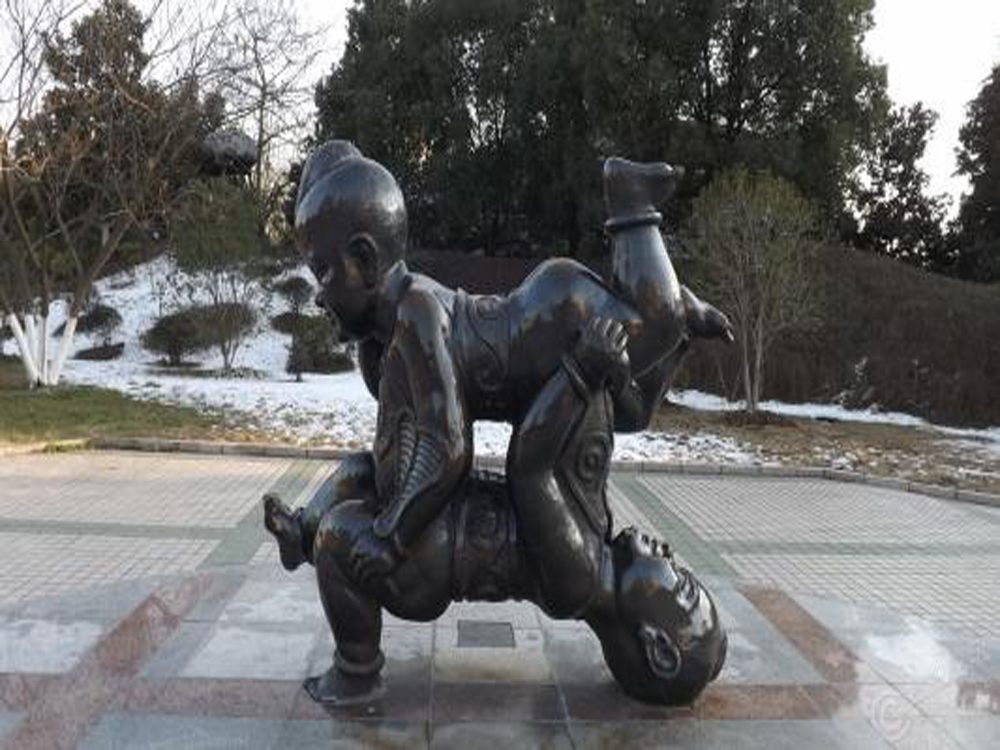
Creating porcelain sculptures with delicate, protruding elements presents a unique set of challenges that test the limits of ceramic artistry. The fragility of porcelain, combined with the structural demands of protruding features, requires meticulous attention at every stage of production.
One primary challenge is material sensitivity. Porcelain’s fine particle structure makes it prone to cracking or warping during drying, especially when thin, extended elements are involved. Artists must carefully control humidity and drying times to prevent stress fractures.
Firing complications also arise. The high temperatures needed to vitrify porcelain can cause protruding sections to slump or distort. Kiln placement and heating rates must be precisely calibrated to ensure even heat distribution. Additionally, the differential shrinkage rates between thick and thin sections often lead to unexpected deformations.
Structural integrity poses another hurdle. Delicate protrusions lack the support of bulkier sections, making them vulnerable to breakage during handling or transportation. Reinforcing these elements without compromising aesthetic appeal requires innovative engineering solutions.
The solution lies in specialized techniques: using paper clay for added flexibility, designing internal support structures, or employing multiple firing stages. Mastering these methods separates exceptional porcelain artists from novices, resulting in breathtaking sculptures that defy their material limitations.