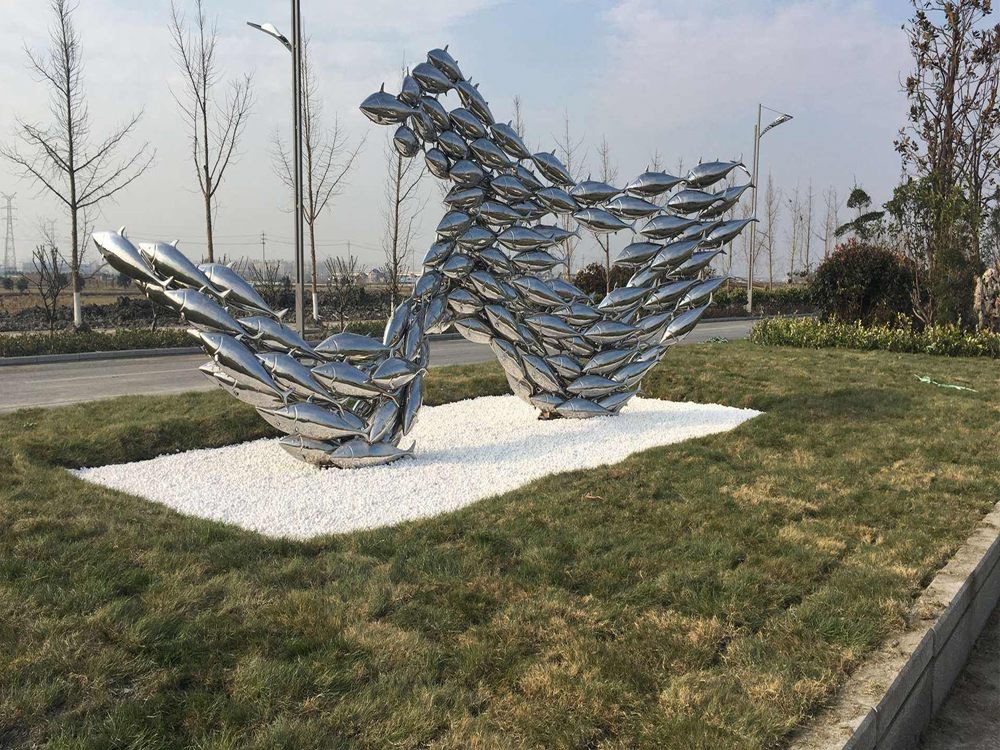
Creating a seamless join between multiple pieces of a porcelain sculpture assembly is a meticulous process that blends technical precision with artistic finesse. Artists begin by carefully designing each component to ensure compatibility in shape, thickness, and drying rate. The edges to be joined are often scored or roughened to enhance adhesion, followed by the application of a slip—a liquid clay mixture—that acts as a bonding agent.
Temperature control during drying and firing is critical. Components are typically dried slowly to prevent warping or cracking, and kiln firing is done in stages to ensure uniform shrinkage. For intricate assemblies, artists may use temporary supports or armatures to maintain alignment until the piece is fully set.
Advanced techniques include using porcelain with similar shrinkage rates or incorporating hidden mechanical supports for larger works. The final step often involves subtle sanding or glazing to erase any visible seams, resulting in a flawless, cohesive artwork that appears as a single, unified creation.
This painstaking approach transforms fragile individual pieces into enduring sculptures, showcasing the artist's mastery over both material and form.