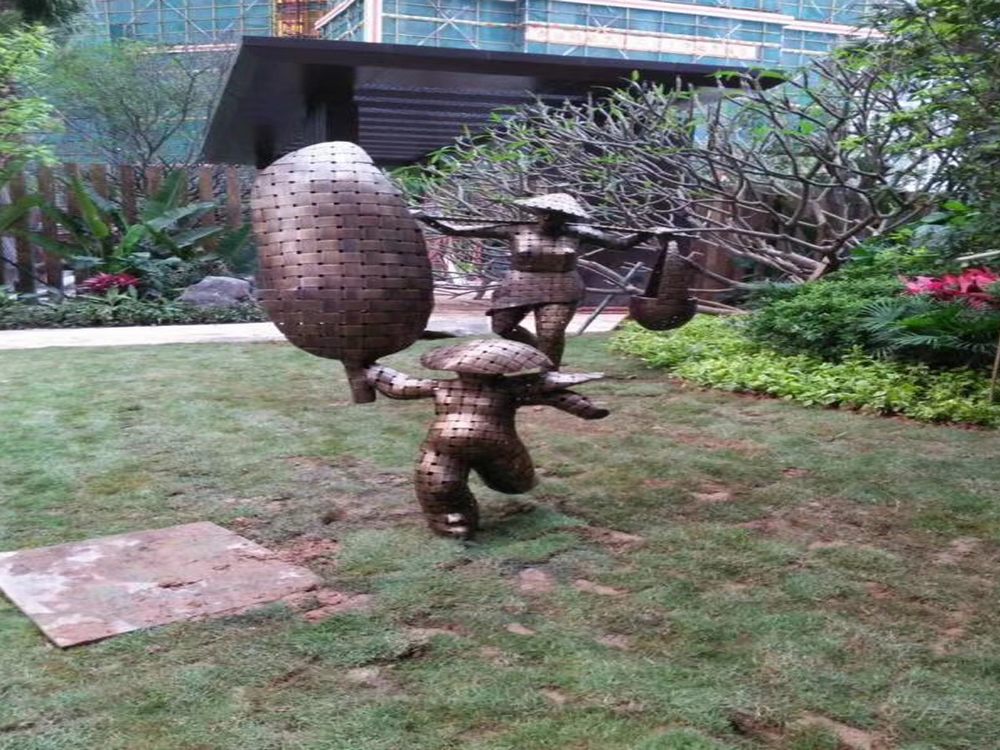
Creating tall porcelain sculptures presents a unique challenge for artists: ensuring structural stability while maintaining aesthetic elegance. The delicate nature of porcelain, combined with the height of these pieces, demands meticulous attention to weight distribution. Artists employ several techniques to overcome this hurdle.
One common method is hollow construction. By crafting the sculpture with a hollow interior, artists reduce overall weight without compromising form. Strategic thickening at the base or along key stress points provides additional support. Some artists incorporate internal armatures made of kiln-safe materials like high-temperature wires or ceramic rods, which reinforce the structure during both creation and firing.
The drying process is equally critical. Uneven drying can cause cracks or collapses, so artists often work in sections, allowing each part to dry thoroughly before assembly. Slow, controlled drying in humidity-controlled environments helps prevent warping.
Glazing and firing also play a role. Multiple thin glaze layers are preferred over thick applications that could add unbalanced weight. During firing, precise temperature control ensures even heat distribution, preventing weak spots.
Ultimately, successful tall porcelain sculptures blend artistic vision with engineering precision, proving that even the most fragile mediums can defy gravity when handled with expertise.