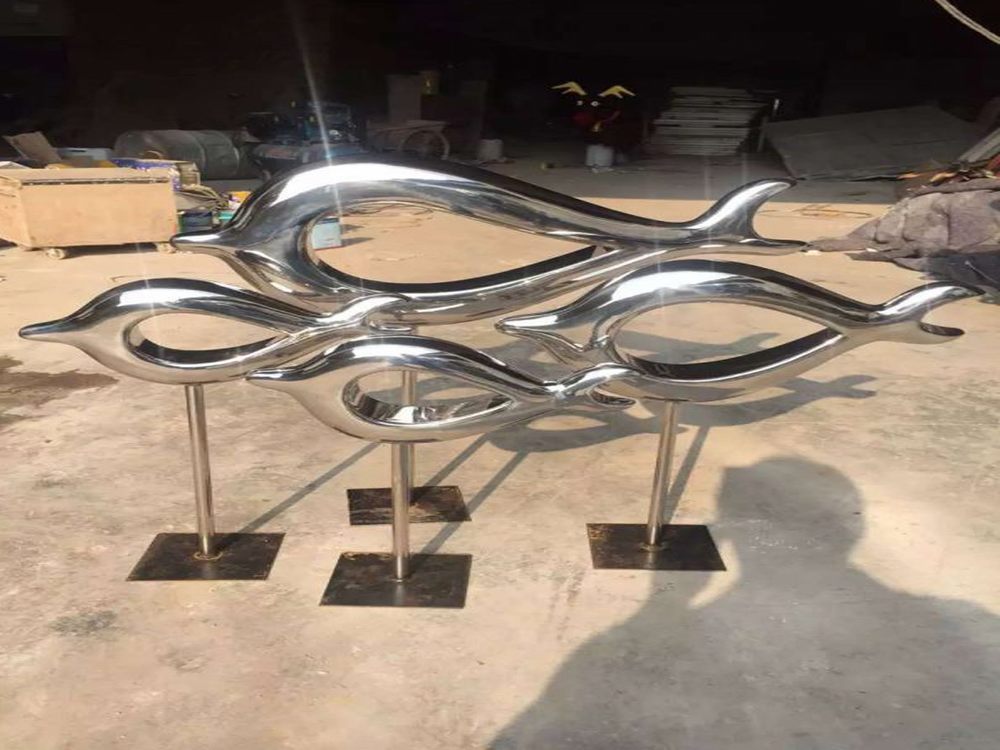
Creating porcelain sculptures with integrated sound-producing elements presents a fascinating yet complex intersection of art and engineering. One primary challenge lies in the inherent fragility of porcelain, which demands meticulous handling during both sculpting and the embedding of sound components. The delicate nature of porcelain can crack or shatter under stress, complicating the integration of mechanisms like small bells or resonating chambers.
Another hurdle is achieving acoustic clarity. Porcelain’s dense structure can dampen or distort sound, requiring precise design adjustments to ensure the desired auditory effect. Artists must experiment with thickness, hollow spaces, and placement of sound elements to optimize resonance without compromising structural integrity.
Additionally, the firing process poses risks. High kiln temperatures may damage electronic components or alter sound-producing materials, necessitating post-firing assembly—a labor-intensive workaround. Balancing aesthetic elegance with functional sound design further tests the artist’s skill, as the visual and auditory elements must harmonize seamlessly.
Ultimately, this fusion of ceramics and sound pushes the boundaries of traditional sculpture, demanding innovation, patience, and a deep understanding of both mediums.