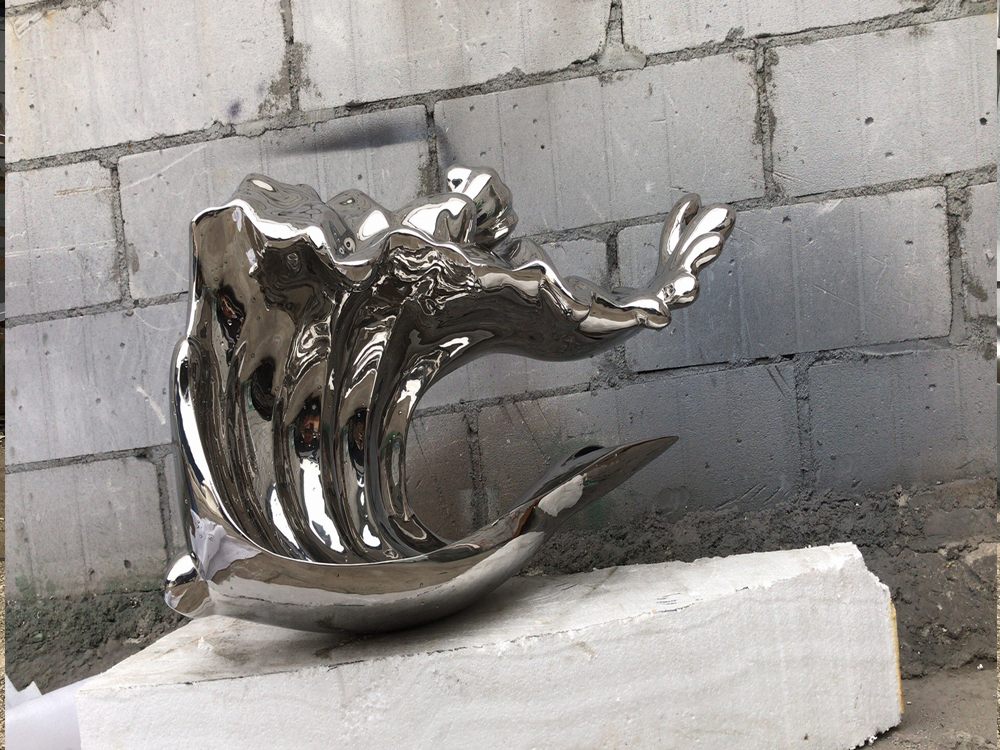
Creating large metal sculptures presents unique challenges, with thermal expansion being a critical concern. As temperatures fluctuate, metal expands and contracts, potentially causing structural stress, warping, or even cracks. Artists employ several strategies to mitigate these effects and ensure their works remain stable over time.
One common approach is the use of expansion joints or gaps between metal sections. These allow the material to move freely without creating tension. For example, welded seams may include small gaps that accommodate movement, while bolted connections can be designed with slotted holes for flexibility.
Material selection also plays a key role. Some metals, like stainless steel or weathering steel, exhibit better resistance to thermal stress. Artists may also incorporate mixed materials, such as combining metal with flexible composites, to absorb movement.
Additionally, structural engineering principles are often applied. Sculptures may be anchored with floating bases or supported by frames that distribute stress evenly. Advanced welding techniques, such as staggered seams, help prevent concentrated stress points.
By thoughtfully integrating these methods, artists ensure their large-scale metal sculptures withstand environmental changes while maintaining aesthetic integrity. Whether displayed outdoors or in temperature-varied spaces, these solutions preserve the longevity and beauty of metal artworks.