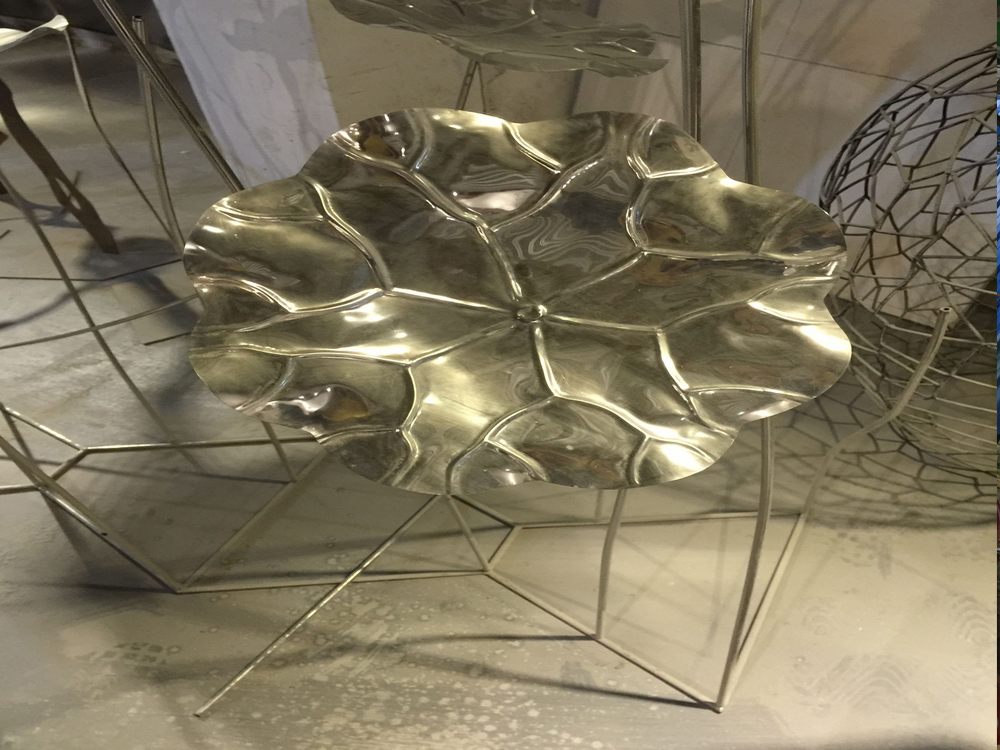
Creating hollow bronze sculptures that maintain structural integrity is a fascinating blend of artistry and engineering. Artists achieve this through centuries-old techniques refined with modern innovations.
The most common method is the lost-wax casting process. First, the artist creates a detailed wax model of the sculpture. This model is then coated in multiple layers of ceramic shell material. Once hardened, the wax is melted away, leaving a hollow ceramic mold. Molten bronze is poured into this cavity, filling the space where the wax once was.
To ensure strength in hollow sculptures, artists employ several strategies:
1. Strategic wall thickness - Maintaining consistent thickness (typically 3-8mm) prevents weak spots
2. Internal supports - Some designs incorporate hidden metal armatures or ribs
3. Quality bronze alloys - Using proper bronze mixtures (typically 90% copper, 10% tin) ensures durability
4. Controlled cooling - Gradual cooling prevents stress fractures
Modern variations include sand casting for larger pieces and digital techniques for precision. The hollow design not only reduces material costs but also makes large sculptures lighter and more transportable.
Through these meticulous processes, artists create breathtaking bronze works that stand the test of time while maintaining their delicate, hollow forms. The balance between hollowness and strength remains one of metalworking's most impressive achievements.