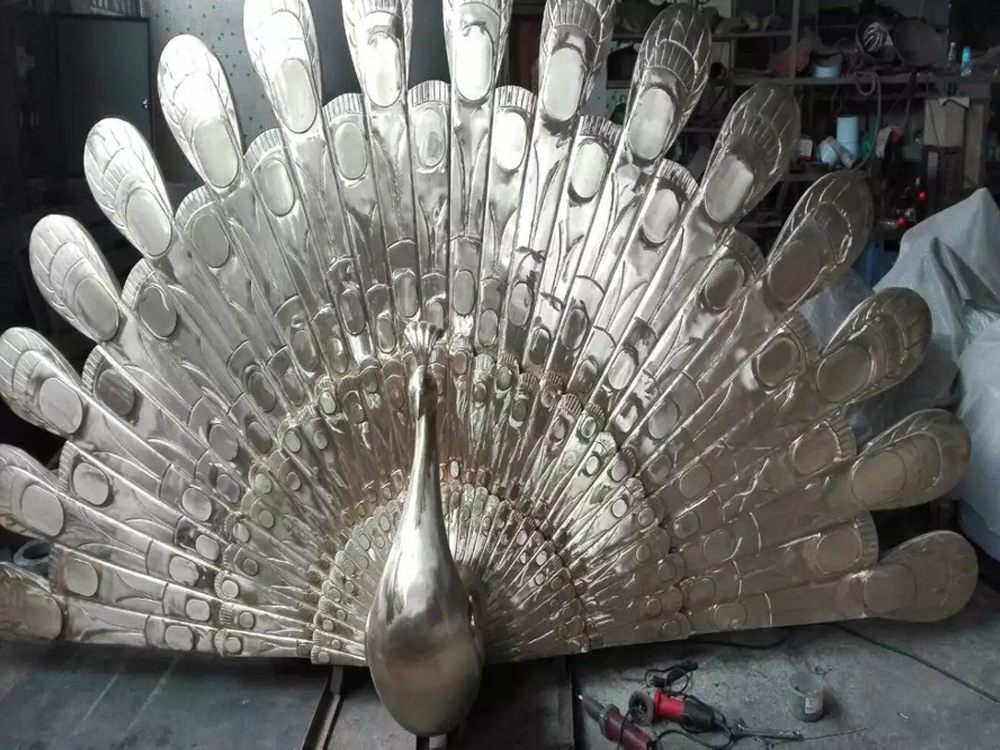
Achieving a uniform patina across multiple editions of a bronze sculpture requires precision, expertise, and careful execution. Here are the most effective techniques to ensure consistency in your bronze artwork:
1. Standardized Chemical Formulas
Use identical patina solutions for each sculpture. Document the exact chemical ratios (e.g., cupric nitrate, ferric nitrate) and application times to replicate results. Pre-mix large batches to avoid variations between editions.
2. Controlled Heat Application
Apply heat evenly with a torch or kiln to activate chemical reactions uniformly. Maintain consistent temperature ranges (typically 150-200°F) across all pieces. Infrared thermometers help monitor surface heat.
3. Layered Application Process
Build the patina in identical stages:
- Clean with degreaser and abrasive pads
- Apply base coat (usually liver of sulfur)
- Add color layers with spray or brush
- Seal with matching wax or lacquer
4. Environmental Controls
Work in a stable environment with controlled humidity (40-60%) and temperature (65-75°F). Sudden changes can alter patina development.
5. Master Reference Sample
Create a "control" sample with your ideal patina. Compare each sculpture to this standard under consistent lighting (daylight 5000K bulbs recommended).
6. Documentation System
Record every step with photos, notes, and material batch numbers. Digital logs ensure perfect replication for future editions.
Professional conservators recommend testing on small bronze plates before full application. Remember that natural variations in bronze alloy composition may require slight adjustments – true consistency comes from systematic processes rather than absolute perfection.