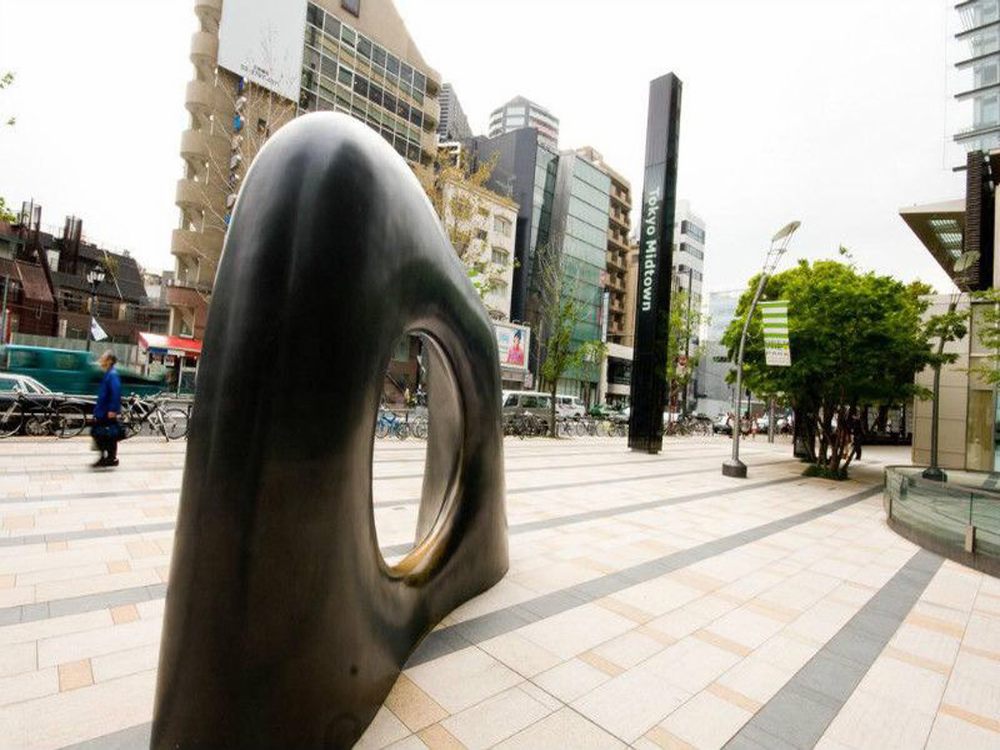
Creating bronze sculptures with fine, delicate features is a demanding art form that presents several unique challenges. One major hurdle is the material itself—bronze's natural viscosity can make it difficult to capture intricate details during casting. Artists often struggle with achieving sharp edges and thin protrusions, as these areas are prone to cracking or warping during cooling.
Another common issue lies in the mold-making process. Fine details like facial expressions or intricate textures require exceptionally precise molds, which can be easily damaged during wax removal or metal pouring. Many sculptors resort to specialized techniques like lost-wax casting or ceramic shell molds to preserve these nuances.
Temperature control also poses significant difficulties. Bronze must be heated to precise temperatures for proper flow into delicate areas, yet excessive heat can destroy fine features. Timing is equally critical; cooling too quickly may cause brittleness, while slow cooling risks distortion.
Surface finishing presents its own set of challenges. Delicate features often require hand-chasing and meticulous polishing, which can accidentally remove or alter important details. Patina application becomes particularly tricky on fine elements, as chemical reactions may appear uneven across different surface depths.
Lastly, structural integrity remains an ongoing concern. Thin, delicate portions are vulnerable to damage during handling or transportation, forcing artists to balance aesthetic goals with practical durability considerations. These combined challenges make delicate bronze sculptures among the most technically demanding works in three-dimensional art.