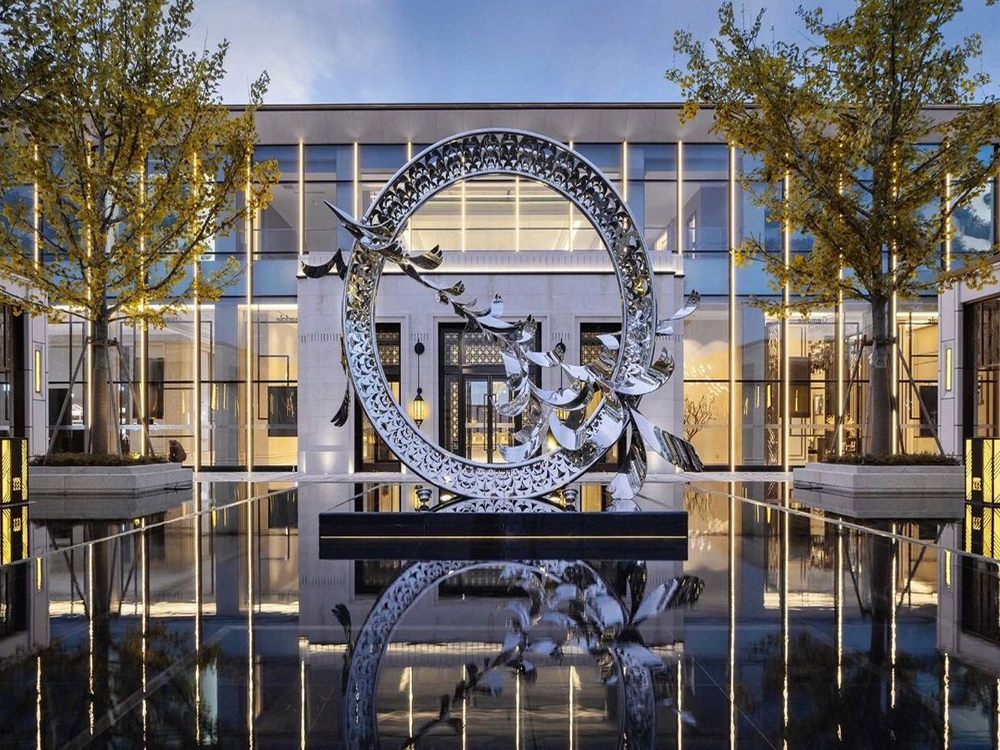
The pricing of finished metal sculptures is deeply intertwined with the fluctuating costs of raw metals, creating a ripple effect across the art market. As primary materials like steel, bronze, aluminum, and copper experience price volatility due to global supply chains, tariffs, and mining conditions, metal artists must constantly adjust their pricing strategies.
High raw material costs directly increase production expenses—sheet metal, rods, and welding supplies may account for 30-50% of a sculpture's final price. Artists often face tough choices: absorb rising costs (reducing profits) or pass them to buyers (risking lower sales). Large-scale sculptures suffer most, as material needs multiply exponentially with size.
Secondary factors compound the impact. Fuel surcharges raise shipping costs for heavy metals, while specialty alloys (like weathering steel or titanium) command premium prices. Some artists mitigate this by using scrap metal, though consistency and quality control become challenges.
Collectors should understand that metal sculpture prices reflect both artistic merit and tangible material realities—a bronze piece's value isn't just aesthetic but tied to literal pounds of commodified metal. As raw material markets grow increasingly unpredictable, this economic dimension will continue shaping the metal art landscape.