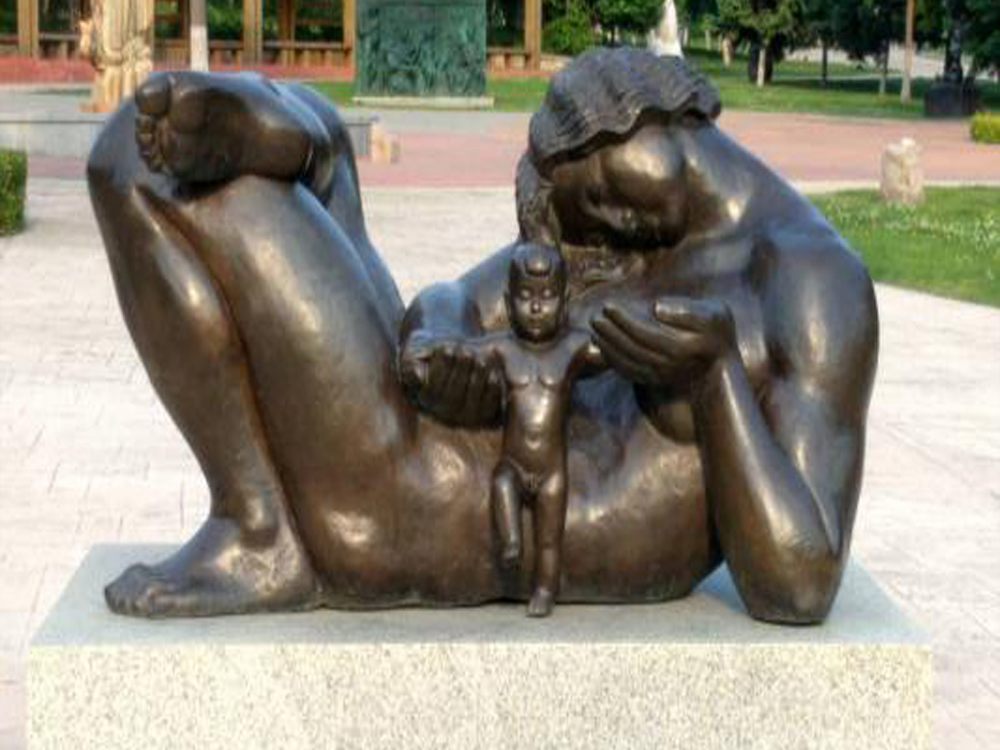
Creating life-sized bronze figures is a complex and demanding artistic endeavor that requires mastery of multiple disciplines. One of the most significant challenges is the initial sculpting process, where artists must work with clay or wax to create a perfect full-scale model that accounts for bronze's unique properties during casting.
The mold-making stage presents another major hurdle, as creating a durable mold capable of capturing intricate details for large sculptures demands exceptional precision. Foundry work introduces further complications, with the bronze pouring process requiring perfect temperature control to avoid defects in massive castings that may weigh hundreds of pounds.
Structural engineering becomes crucial for life-sized works, as artists must ensure the sculpture can support its own weight while maintaining artistic integrity. The metal's expansion and contraction during cooling can distort details or cause cracking if not properly managed.
Finishing these monumental pieces presents additional obstacles, from chasing and welding seams to applying patinas evenly across large surfaces. The sheer physical scale of the work demands specialized equipment and facilities that many artists lack.
Environmental factors like temperature fluctuations during outdoor installations and long-term maintenance against corrosion add to the challenges. Each of these hurdles requires specialized knowledge, making the creation of life-sized bronze figures one of the most technically demanding forms of sculptural art.