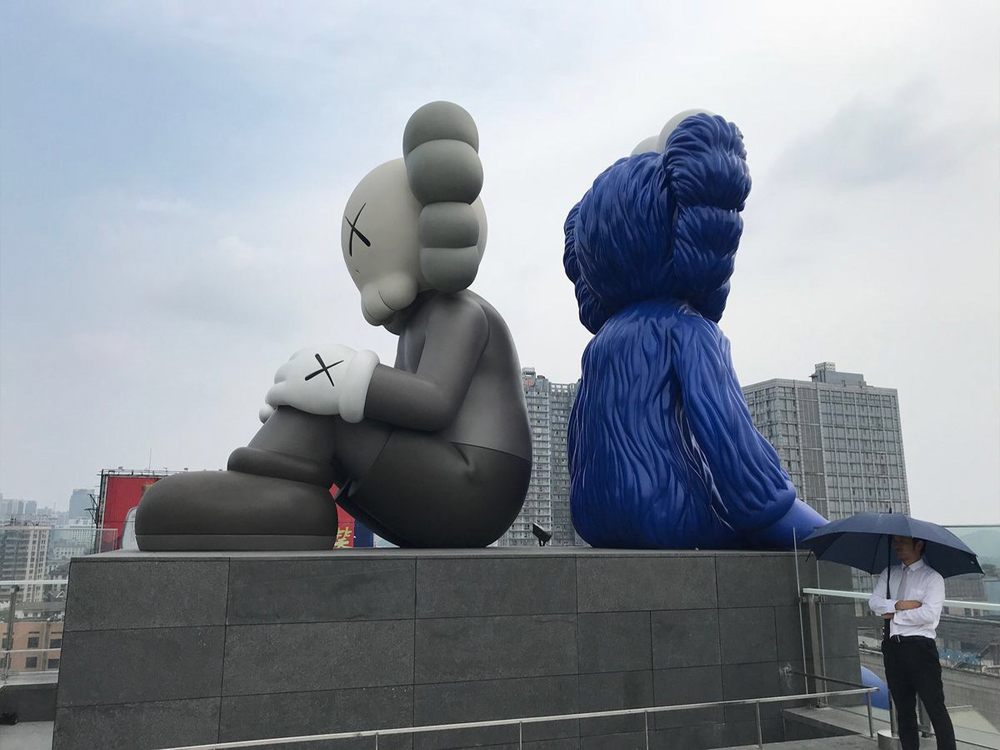
Bronze sculpture production relies heavily on mold-making techniques to achieve intricate details and durability. Among the most common types of molds used are the lost wax casting method, sand casting, and ceramic shell molds.
The lost wax casting process, also known as investment casting, involves creating a wax model coated in a ceramic shell. Once the wax is melted away, molten bronze is poured into the cavity, resulting in highly detailed sculptures. This method is favored for its precision and ability to capture fine artistic expressions.
Sand casting, on the other hand, uses compacted sand to form molds. While less detailed than lost wax, it is cost-effective and ideal for larger sculptures. The sand mold is reusable, making it a practical choice for industrial applications.
Ceramic shell molds combine elements of both techniques, offering a balance between detail and strength. A refractory ceramic material is layered over a wax model, creating a sturdy mold capable of withstanding high temperatures during bronze pouring.
Each mold type has unique advantages, allowing artists to choose based on project requirements, budget, and desired finish. Understanding these methods is essential for anyone involved in bronze sculpture production.