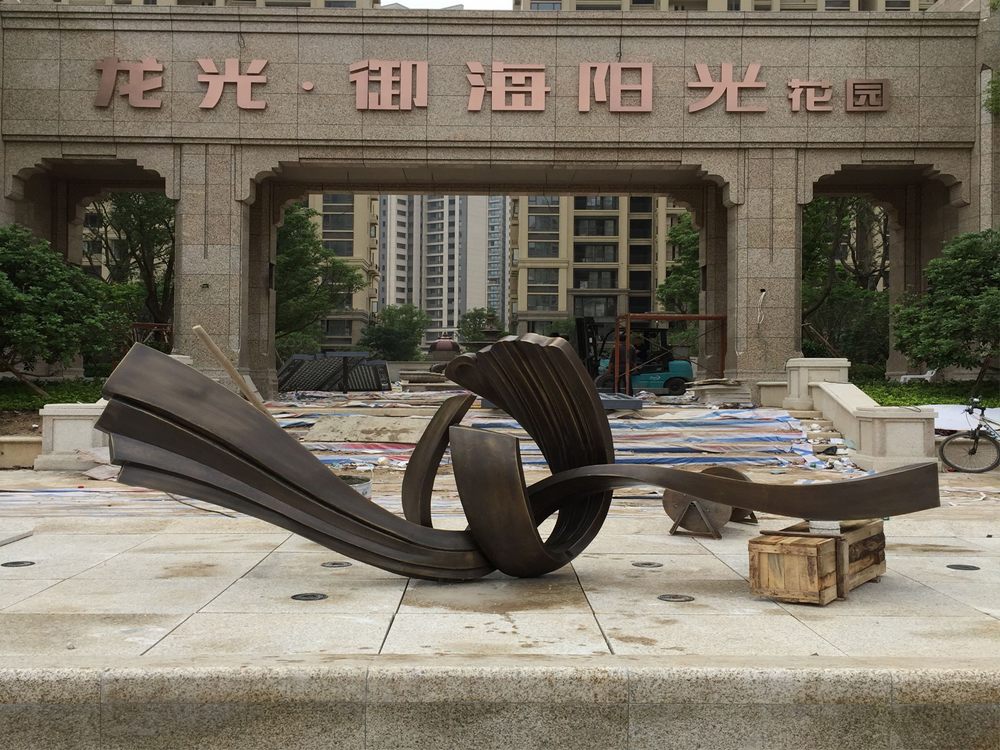
Creating a mold for bronze sculpture casting is a crucial step in bringing artistic visions to life. Several techniques are widely used, each offering unique advantages depending on the project's complexity and desired finish.
1. Lost Wax Casting
The most traditional and precise method, lost wax casting involves sculpting the original model in wax, coating it with a ceramic shell, and then melting the wax away to leave a hollow mold. Molten bronze is poured into this cavity, resulting in highly detailed sculptures.
2. Sand Casting
Ideal for larger or simpler designs, sand casting uses compacted sand to form the mold. A pattern is pressed into the sand, removed, and bronze is poured into the impression. While less detailed than lost wax, it’s cost-effective for bulk production.
3. Ceramic Shell Casting
A modern variation of lost wax, ceramic shell casting involves dipping the wax model in a liquid ceramic slurry multiple times to build a sturdy shell. This method is favored for its durability and ability to capture fine details.
4. Plaster Mold Casting
Plaster molds are used for smaller or experimental pieces. The original model is encased in plaster, which is then removed after hardening. Though less durable, plaster allows for quick iterations.
5. Rubber Mold Casting
Flexible rubber molds are perfect for intricate designs with undercuts. A silicone or urethane rubber mold is made from the original model, enabling multiple bronze castings without losing detail.
Each method has its strengths, and artists often choose based on scale, budget, and artistic requirements. Understanding these techniques ensures the best results for stunning bronze sculptures.