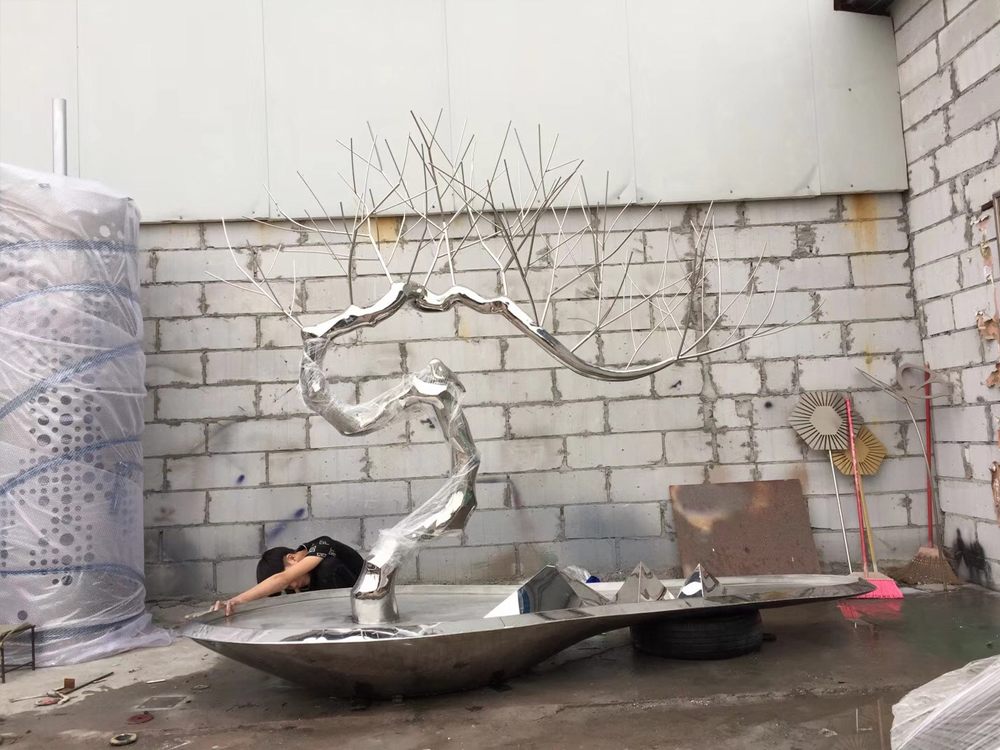
Creating hollow bronze sculptures is a revered art form that combines craftsmanship and metallurgical expertise. Among the most common techniques, lost wax casting stands out as a time-honored method. This process involves sculpting a wax model, encasing it in a refractory mold, and melting the wax away to leave a cavity for molten bronze.
Another widely used method is sand casting, where a sculpture is pressed into compacted sand to form a mold. The sand mold is then filled with bronze, offering a cost-effective solution for larger pieces.
Ceramic shell casting is a modern adaptation, where layers of ceramic slurry are applied to a wax model. Once hardened, the shell is fired, melting the wax and creating a precise mold for bronze pouring.
Artists may also employ direct metal fabrication, welding or assembling pre-cast bronze sections to achieve hollow structures. Each technique offers unique advantages, from intricate detail in lost wax casting to the scalability of sand casting. Mastering these methods allows sculptors to bring their visionary works to life in enduring bronze.