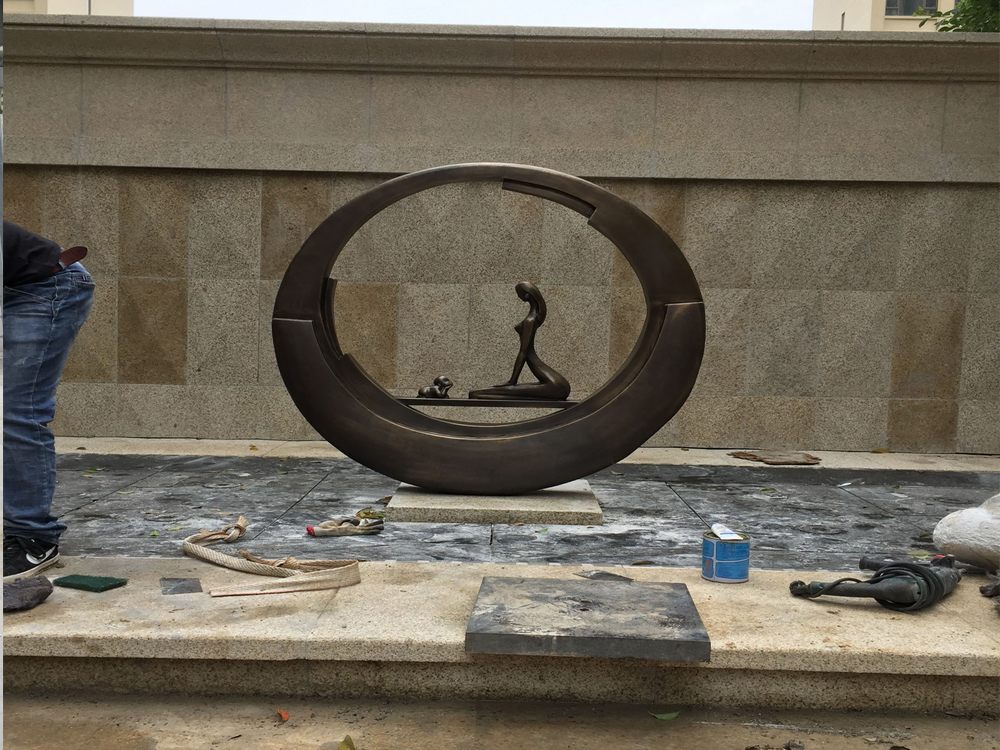
Metal sculptors employ a variety of methods to source their materials, often balancing creativity with budget constraints. Many artists rely on scrap yards and recycling centers, where discarded metal pieces—such as old car parts, machinery components, or construction remnants—can be repurposed at a low cost. Others purchase new materials from industrial suppliers, opting for metals like steel, bronze, or aluminum, which offer durability but come at a higher price.
The cost implications vary significantly depending on the source and type of metal. Recycled materials are economical but may require extensive cleaning and preparation. New metals, while more expensive, provide consistency and quality, ideal for large-scale or commissioned works. Additionally, specialty metals like titanium or copper can drive costs up further due to their rarity and processing requirements.
Some sculptors also collaborate with manufacturers or construction firms to obtain surplus or off-cut materials, reducing expenses while fostering sustainable practices. Ultimately, the choice of material impacts not only the budget but also the artistic process, as different metals demand distinct tools and techniques for shaping and finishing.
By understanding these sourcing strategies and cost factors, aspiring metal sculptors can make informed decisions that align with their artistic vision and financial resources.