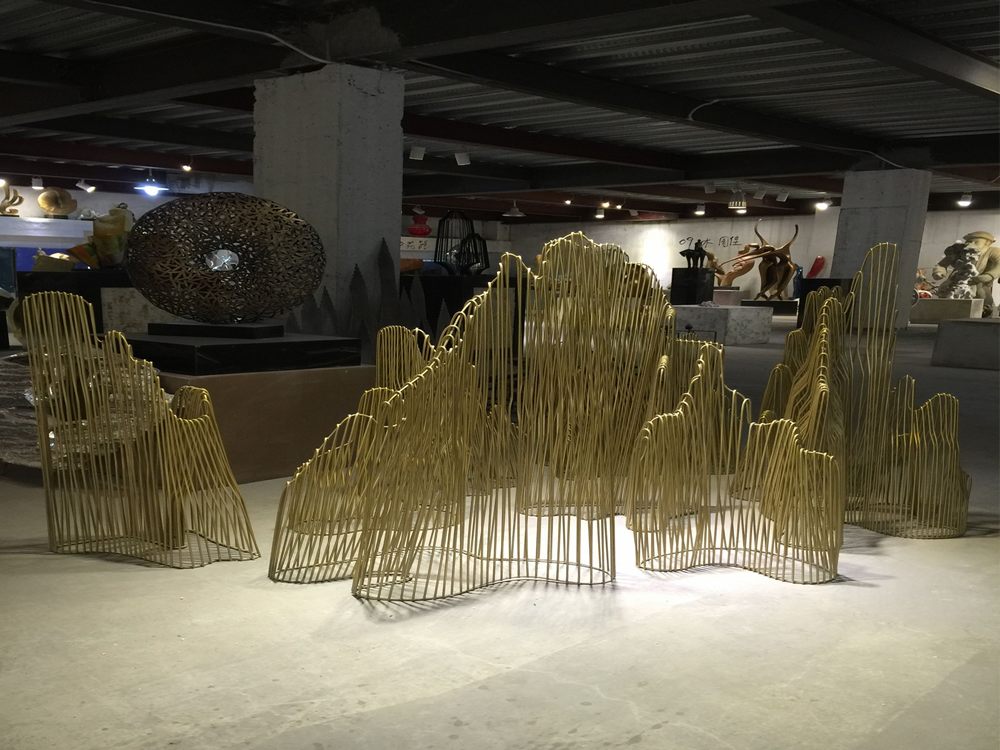
Thermal cracking in welded joints is a common issue that compromises structural integrity. To prevent it, follow these proven methods:
1. Preheat the Base Metal: Preheating reduces thermal stress by minimizing temperature differences between the weld and surrounding material.
2. Control Heat Input: Use appropriate welding techniques like pulsed arc welding to manage heat distribution and avoid excessive thermal gradients.
3. Select Suitable Filler Materials: Choose low-hydrogen electrodes or filler metals with compatible thermal expansion coefficients to minimize cracking risks.
4. Post-Weld Heat Treatment (PWHT): Stress-relieving treatments like annealing help redistribute residual stresses and prevent crack formation.
5. Optimize Joint Design: Avoid sharp corners and ensure proper groove angles to reduce stress concentration points.
6. Monitor Cooling Rates: Slow cooling using insulating blankets or controlled environments prevents rapid contraction-induced cracks.
By implementing these strategies, welders can significantly reduce thermal cracking risks, ensuring stronger and more reliable joints.