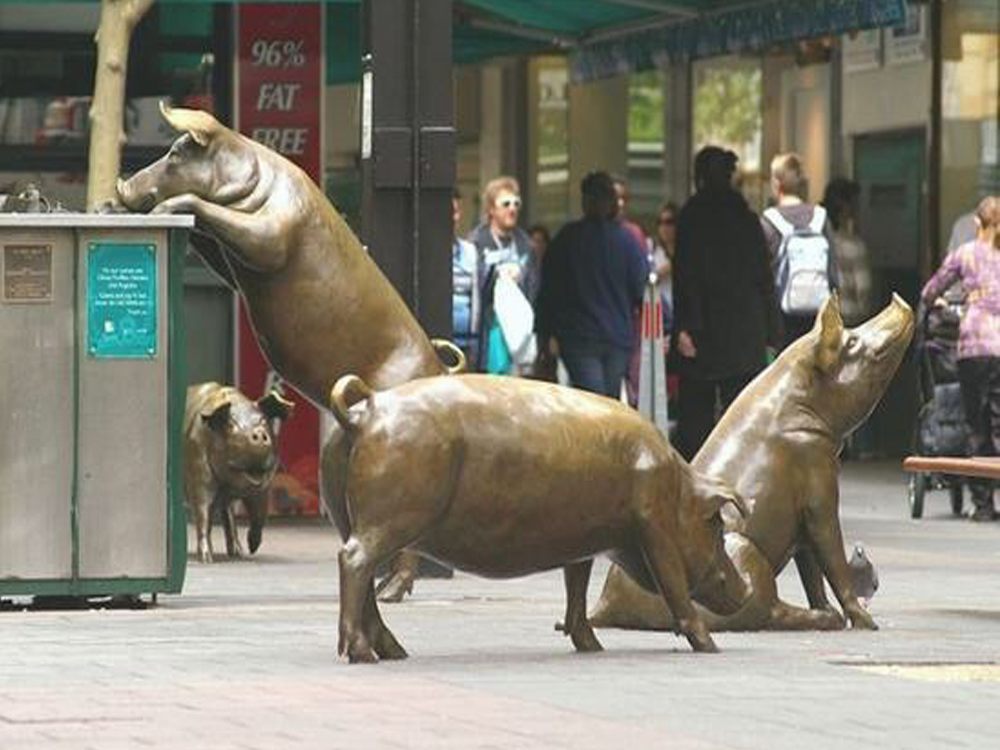
Thermal fatigue in welded joints is a common issue that can lead to premature failure in structures exposed to cyclic heating and cooling. To mitigate this problem, several proven strategies can be implemented.
1. Material Selection: Choose alloys with high thermal conductivity and low thermal expansion coefficients to reduce stress buildup during temperature fluctuations.
2. Optimized Welding Techniques: Employ low-heat-input welding methods like pulsed MIG or TIG welding to minimize residual stresses and distortion.
3. Post-Weld Heat Treatment (PWHT): Stress-relieving heat treatments can significantly reduce residual stresses that contribute to thermal fatigue cracking.
4. Controlled Cooling Rates: Implement gradual cooling processes to prevent rapid temperature changes that induce thermal stresses.
5. Design Improvements: Incorporate flexible joint designs that allow for thermal expansion without creating stress concentrations.
6. Surface Treatments: Shot peening or laser shock peening can introduce beneficial compressive stresses to counteract thermal fatigue effects.
7. Regular Inspection: Implement non-destructive testing methods to detect early signs of thermal fatigue before catastrophic failure occurs.
By combining these approaches, engineers can significantly extend the service life of welded components operating in thermal cycling environments. The most effective prevention strategy often involves a combination of proper material selection, optimized welding procedures, and appropriate post-weld treatments tailored to the specific application requirements.