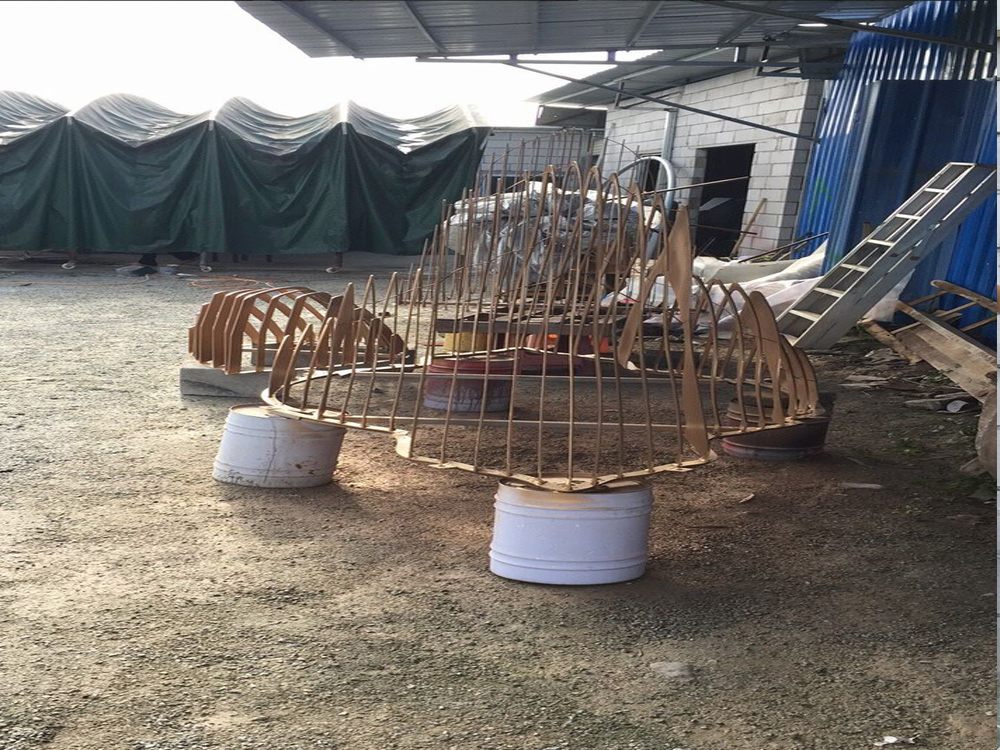
The creation of large metal sculptures is a fascinating intersection of art and engineering, where creative vision meets structural practicality. Artists often rely on engineers to ensure their monumental works can withstand environmental forces while maintaining aesthetic intent. This collaboration typically follows an iterative process:
1. Conceptual Phase: Artists present initial designs to engineers, who assess feasibility regarding weight distribution, material stress, and wind resistance. Early feedback may lead to adjustments in proportions or support systems.
2. Material Selection: Engineers advise on suitable metals (e.g., stainless steel vs. corten) based on durability, weldability, and maintenance requirements. This impacts both the sculpture's longevity and visual texture.
3. Structural Refinement: Digital modeling and stress simulations help identify weak points. Engineers might suggest adding internal reinforcements or altering joint designs, while artists preserve critical visual elements.
4. Fabrication Adjustments: During welding and assembly, real-world challenges emerge. Engineers provide on-site solutions for unexpected issues like thermal expansion or load-bearing miscalculations.
Successful collaborations thrive on mutual respect—artists embrace technical constraints as creative opportunities, while engineers learn to interpret artistic intent through an analytical lens. Notable examples include Richard Serra’s tilted steel plates (where engineers calculated precise angles to prevent toppling) and Anish Kapoor’s reflective surfaces (requiring metallurgists to achieve flawless finishes).
Ultimately, this synergy transforms raw metal into enduring art, proving that great sculptures are born not just from inspiration, but from the alchemy of imagination and physics.