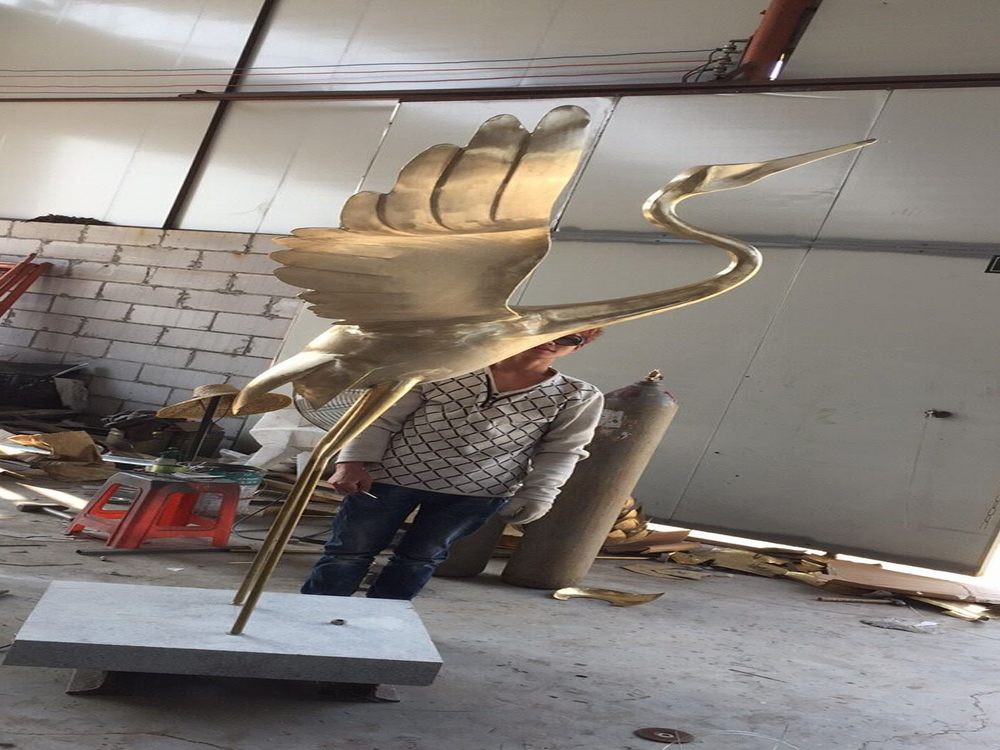
Collaborating with foundries in the casting process is critical for achieving high-quality metal components while maintaining efficiency and cost-effectiveness. Here are the best practices to ensure a successful partnership:
1. Clear Communication – Establish open and frequent communication channels to align on project requirements, timelines, and quality standards. Detailed technical drawings and specifications help minimize errors.
2. Early Involvement – Engage the foundry early in the design phase to leverage their expertise in material selection, manufacturability, and cost optimization.
3. Quality Assurance Protocols – Implement rigorous quality control measures, including material testing, dimensional inspections, and defect analysis, to ensure consistency.
4. Process Transparency – Request regular updates on production progress and potential challenges. Transparency fosters trust and allows for proactive problem-solving.
5. Long-Term Partnership Mindset – Treat the foundry as a strategic partner rather than just a supplier. Building long-term relationships leads to better pricing, priority scheduling, and continuous improvement.
By following these best practices, manufacturers can optimize their casting processes, reduce waste, and enhance product reliability through strong foundry collaboration.