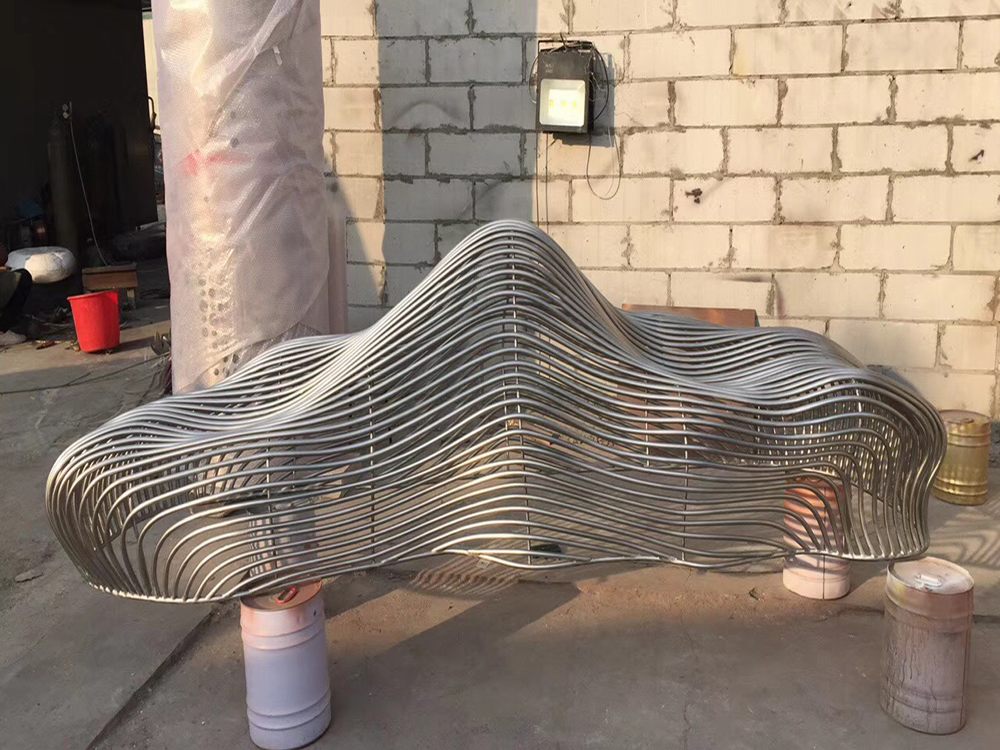
Stress fractures in welded metal joints can compromise structural integrity and lead to costly repairs. To prevent these issues, follow these best practices:
1. Material Selection – Choose metals with compatible thermal expansion rates to minimize residual stress. High-quality base materials reduce the risk of cracking.
2. Proper Welding Techniques – Use preheating to reduce thermal shock and control cooling rates. Employ low-hydrogen electrodes to prevent hydrogen-induced cracking.
3. Joint Design Optimization – Avoid sharp corners and abrupt transitions. Smooth, gradual weld profiles distribute stress more evenly.
4. Post-Weld Heat Treatment (PWHT) – Stress-relieving treatments like annealing or tempering can reduce residual stresses and enhance joint durability.
5. Regular Inspection & Testing – Non-destructive testing (NDT) methods, such as ultrasonic or X-ray inspection, help detect early signs of stress fractures.
By implementing these strategies, welders and engineers can significantly reduce the likelihood of stress fractures, ensuring long-lasting and reliable metal joints.