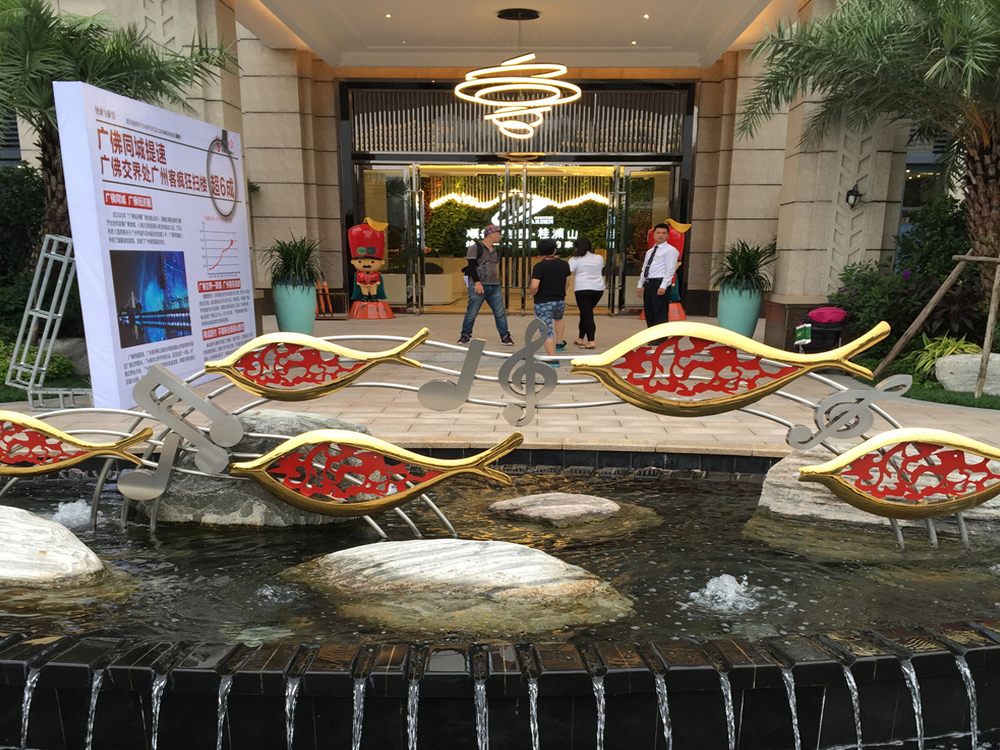
Intergranular corrosion is a common issue in welded metal sculptures, often leading to structural weakness and aesthetic degradation. To prevent this, artists and fabricators must adopt a combination of material selection, welding techniques, and post-weld treatments.
1. Material Selection: Opt for corrosion-resistant alloys like 316L stainless steel or duplex stainless steels, which contain low carbon content and added molybdenum to resist intergranular attack.
2. Welding Techniques: Use low-heat input methods such as TIG (Tungsten Inert Gas) welding to minimize the risk of carbide precipitation at grain boundaries. Avoid prolonged exposure to high temperatures during welding.
3. Post-Weld Heat Treatment (PWHT): Apply solution annealing or quenching to dissolve carbides and restore the alloy’s corrosion resistance. This is especially critical for austenitic stainless steels.
4. Proper Cleaning and Passivation: After welding, remove contaminants and oxides using acid pickling or electrochemical passivation to enhance the metal’s natural protective layer.
5. Design Considerations: Avoid crevices and stagnant areas where corrosive agents can accumulate. Ensure proper drainage and ventilation in the sculpture’s design.
By integrating these methods, artists can create durable, corrosion-resistant metal sculptures that withstand environmental challenges while maintaining their artistic integrity.