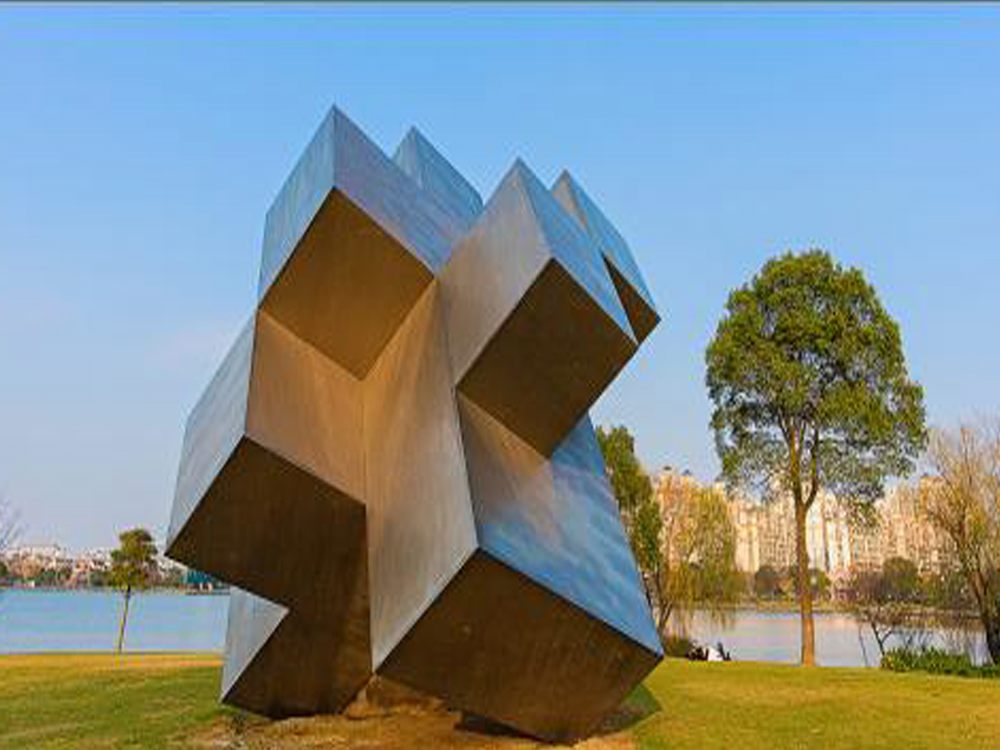
Creating kinetic metal sculptures that withstand the test of time while incorporating moving parts requires both artistic vision and engineering precision. Artists employ several innovative techniques to achieve this delicate balance between motion and durability.
One fundamental approach involves using high-quality, corrosion-resistant metals like stainless steel, bronze, or aluminum alloys. These materials not only endure outdoor elements but also maintain structural integrity despite constant movement. Many artists treat surfaces with protective coatings to prevent wear at friction points.
For the moving components, sculptors often implement bearing systems similar to those used in industrial machinery. Precision ball bearings or sleeve bearings allow smooth motion while minimizing wear. Some artists create their own specialized pivot points using hardened metal pins rotating within brass bushings.
The design phase is crucial, with many artists creating small-scale prototypes to test movement patterns and stress points. Computer-aided design (CAD) software helps simulate forces and identify potential weak spots before fabrication begins. Weight distribution plays a critical role - balanced components reduce strain on moving parts.
Maintenance considerations are built into the design. Accessible lubrication points, replaceable wear components, and modular construction allow for repairs without compromising artistic integrity. Some artists incorporate weather-resistant covers for sensitive mechanisms in outdoor installations.
Advanced techniques include using magnetic levitation for frictionless movement or shape-memory alloys that respond to temperature changes. These innovative approaches eliminate traditional wear points while creating mesmerizing motion effects.
By combining robust materials, mechanical engineering principles, and thoughtful design, artists create kinetic metal sculptures that move gracefully for years, proving that dynamic art can indeed stand the test of time.