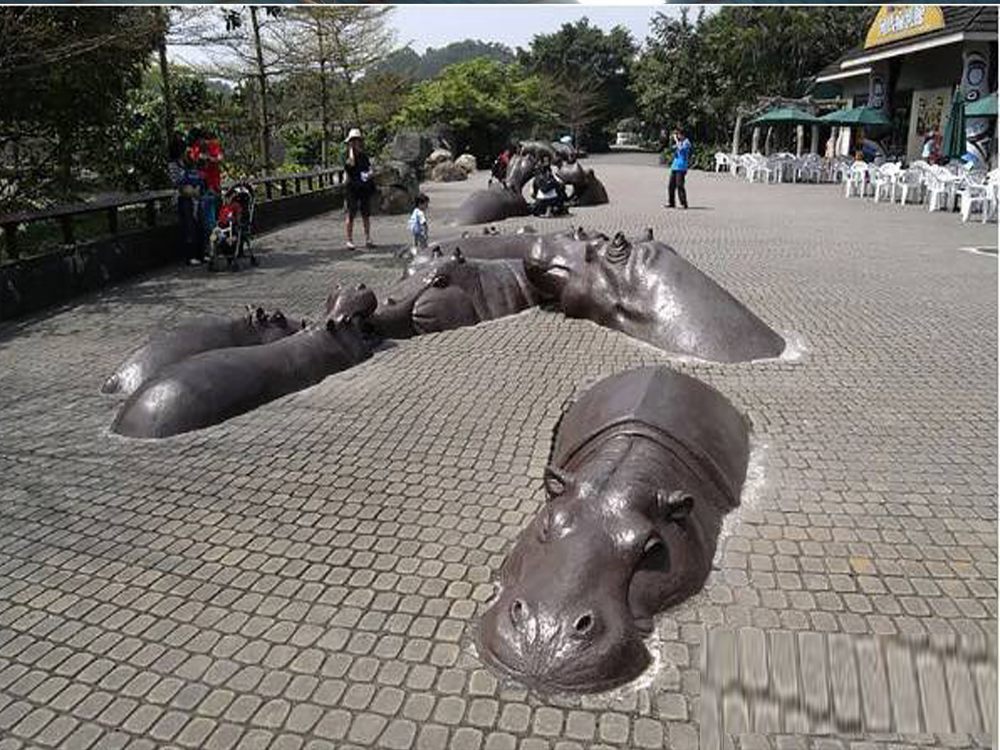
Creating metal sculptures for high-vibration environments presents unique challenges that test the limits of artistic and engineering expertise. The constant stress from vibrations demands meticulous material selection—traditional metals may fatigue or crack over time, requiring alloys with higher tensile strength or composite materials. Structural design becomes critical; artists must balance aesthetics with reinforced joints, shock-absorbing bases, and strategic weight distribution to prevent resonance effects.
Welding techniques must evolve beyond standard practices, as vibration can weaken seams. Many sculptors adopt aerospace-grade fastening methods or flexible interlocking components. Environmental factors like temperature fluctuations in industrial settings further complicate material behavior, necessitating protective coatings or thermal expansion allowances.
Maintenance accessibility becomes part of the artwork’s DNA—hidden inspection ports or modular sections allow for tightening and repairs without compromising visual impact. Perhaps most challenging is preserving artistic vision while accommodating these technical demands, transforming constraints into innovative design features that make vibration-resistant sculptures uniquely captivating.