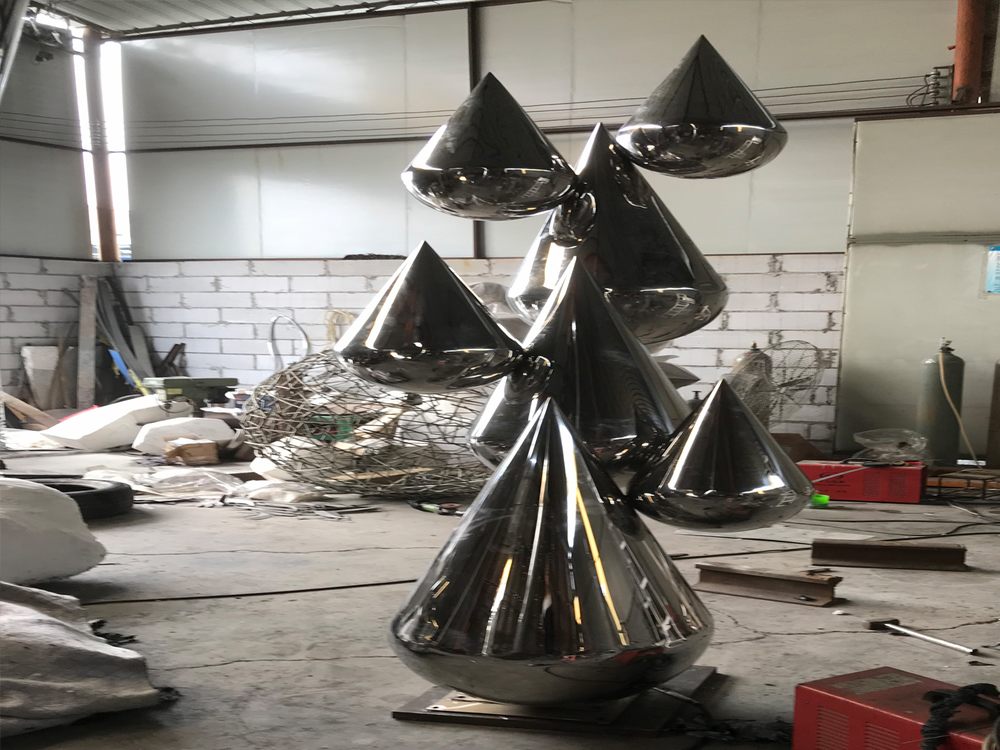
Sculptors often face the challenge of installing large or intricate works, especially in public spaces or exhibitions. Modular designs offer a practical solution by breaking down complex sculptures into smaller, manageable components. These pre-fabricated modules are designed to fit together seamlessly, reducing on-site assembly time and minimizing errors.
One key advantage of modularity is its adaptability. Sculptors can transport sections individually, easing logistical constraints. For example, a towering metal sculpture might be divided into interlocking segments, each crafted to precise specifications. This approach also allows for easier repairs or modifications, as individual modules can be replaced without dismantling the entire piece.
Additionally, modular designs enable collaborative workflows. Different artists or fabricators can work on separate modules simultaneously, speeding up production. This technique is particularly valuable for time-sensitive projects or when working with materials like ceramics or glass that require specialized kiln firings.
Beyond practicality, modularity can become an artistic statement. Some sculptors intentionally highlight the joins between modules, turning structural necessity into aesthetic feature. Others use interchangeable modules to create dynamic, ever-changing installations.
By embracing modular strategies, sculptors balance creative ambition with technical feasibility, ensuring their visions can be realized and installed efficiently, even at monumental scales.