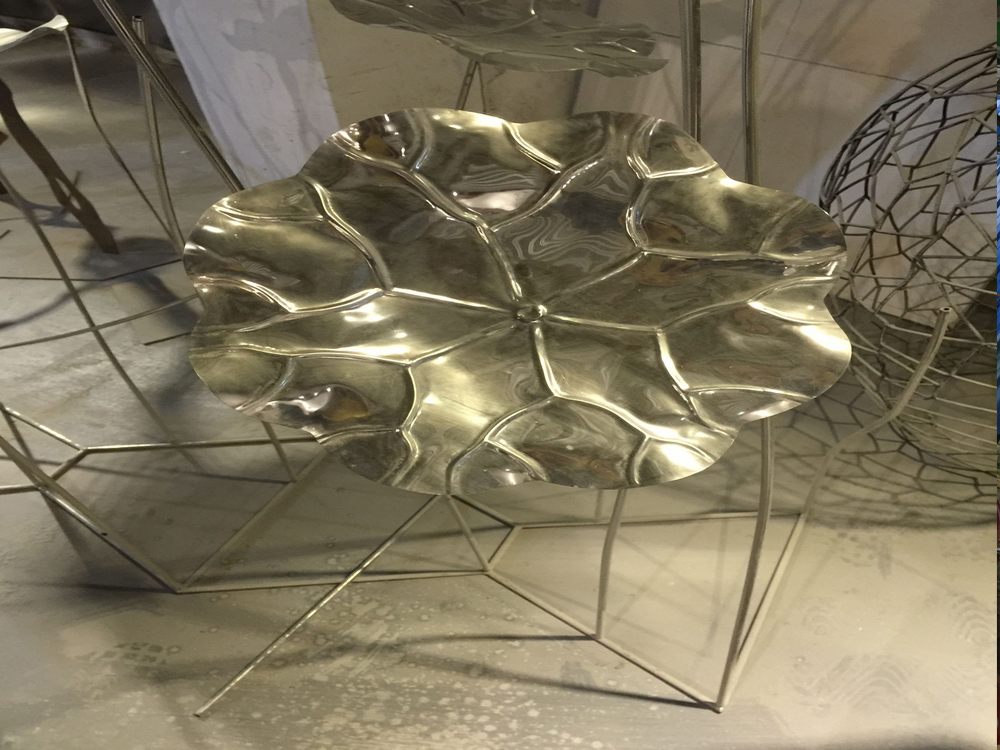
Creating metal sculptures is a complex and rewarding artistic process, but it comes with unique challenges. One of the most common issues artists face is material selection—choosing the right metal that balances durability, malleability, and cost. Stainless steel offers strength but requires specialized tools, while copper is softer but may oxidize over time.
Welding and joining techniques present another hurdle. Achieving seamless connections without warping the metal demands precision and experience. Many sculptors struggle with heat distortion, which can alter the intended shape of the piece. Proper heat management and sequential welding are crucial solutions.
Structural integrity is equally important, especially for large-scale works. Artists must calculate weight distribution and support systems to prevent collapse. This often involves hidden armatures or strategic bracing that maintains the sculpture's aesthetic while ensuring stability.
Surface finishing poses its own set of challenges. Achieving the desired texture—whether polished, patinated, or rusted—requires mastery of chemical treatments and protective coatings. Environmental factors like humidity can unpredictably affect these processes.
Lastly, the high cost of materials and equipment limits many artists. Creative problem-solving, like using recycled metals or collaborating with fabrication studios, helps overcome budget constraints while maintaining artistic vision.
By understanding these common obstacles, metal sculptors can better prepare for their projects and develop innovative solutions that elevate their craft.