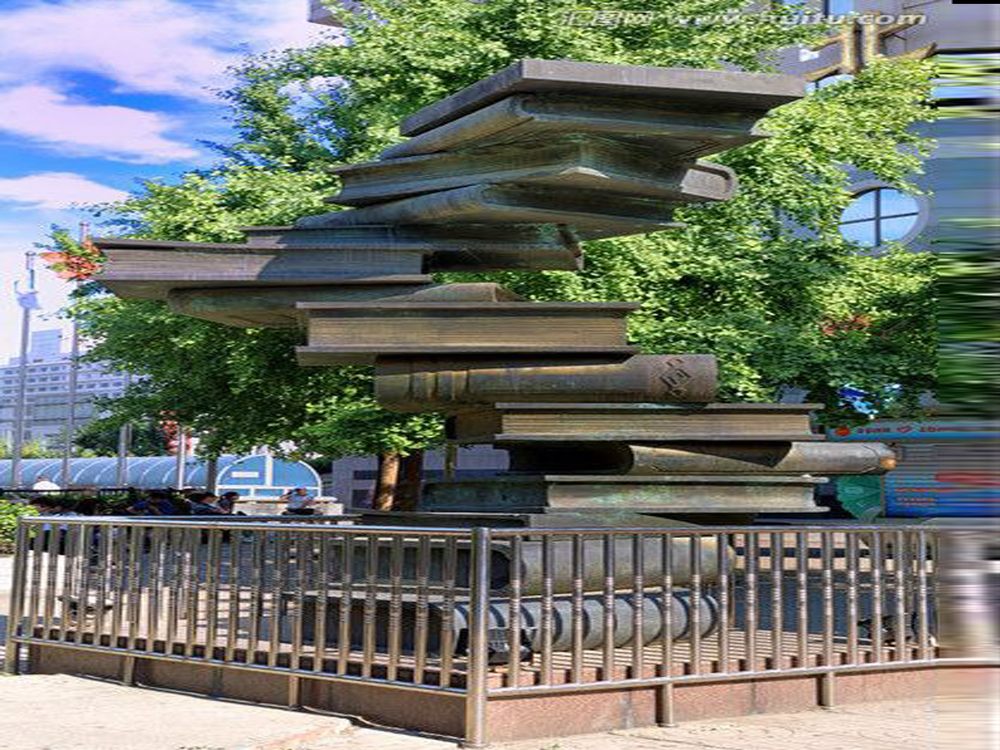
Metal sculptures captivate audiences with their artistic expression, but their engineering principles vary significantly between static and kinetic forms. Static metal sculptures rely on rigid structural integrity, requiring robust foundations and load-bearing calculations to withstand environmental forces like wind and gravity. Engineers prioritize material strength, weld quality, and corrosion resistance in these immobile artworks.
Kinetic sculptures introduce dynamic engineering challenges. They incorporate movement mechanisms such as bearings, pivots, or motorized components, demanding precise balance and friction management. Material selection must account for repetitive motion wear, while aerodynamic considerations become crucial for wind-powered pieces. The engineering focuses on creating reliable motion patterns while maintaining artistic vision.
Structural complexity differs markedly. Static pieces often use triangulation and weight distribution techniques, whereas kinetic works require motion trajectory analysis and often employ counterweights. Maintenance requirements also diverge - kinetic sculptures need regular lubrication and part replacements, while static works primarily require surface treatments.
From an engineering perspective, kinetic sculptures represent a marriage of mechanical design and artistic expression, pushing boundaries in material science and motion physics. Static sculptures, while seemingly simpler, demand equal engineering rigor to ensure longevity and stability in their stationary form. Both types showcase how engineering principles elevate metal art from concept to enduring cultural artifact.