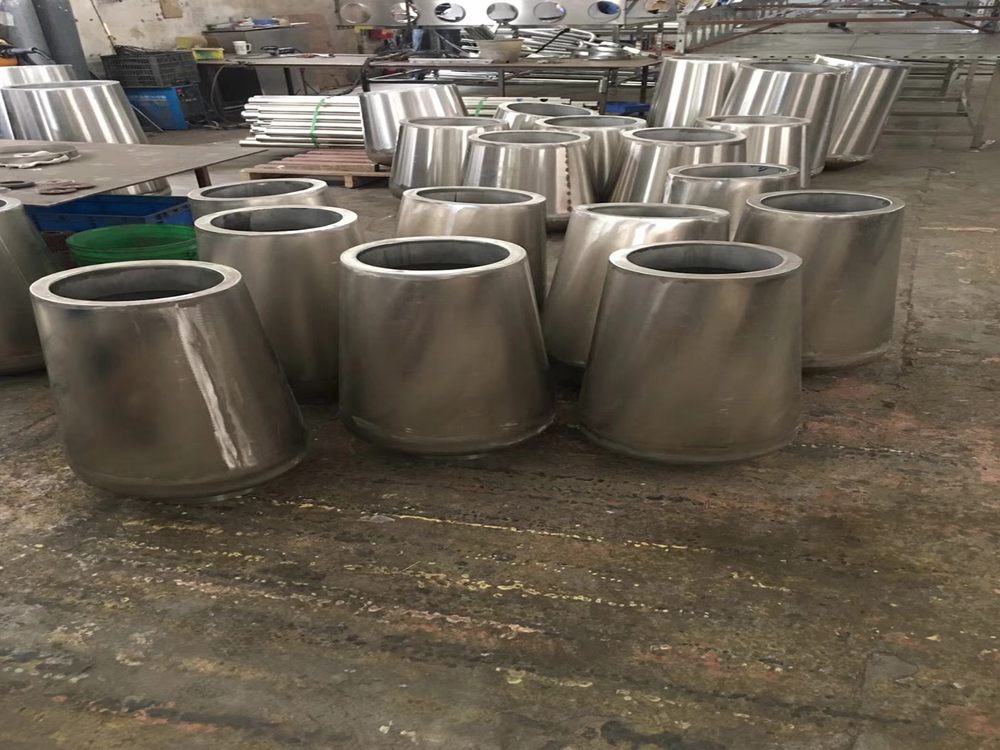
Creating large-scale metal sculptures requires a blend of artistic vision and technical expertise, with welding playing a pivotal role in bringing these monumental works to life. Several welding techniques are commonly employed, each offering unique advantages depending on the sculpture's design, material, and structural demands.
1. MIG Welding (Metal Inert Gas):
MIG welding is favored for its speed and versatility, making it ideal for large sculptures requiring long, continuous welds. It works well with materials like steel and aluminum, providing strong, clean joints.
2. TIG Welding (Tungsten Inert Gas):
TIG welding offers precision and control, perfect for intricate details or thinner metals. Its ability to produce high-quality, aesthetically pleasing welds makes it a top choice for sculptors prioritizing fine craftsmanship.
3. Arc Welding (Stick Welding):
Known for its robustness, arc welding is often used for outdoor sculptures exposed to harsh weather. It’s effective on thicker metals and can handle less-than-ideal conditions, though it requires more skill to achieve clean results.
4. Gas Welding (Oxy-Acetylene):
While less common today, gas welding allows for delicate, controlled heat application, useful for smaller sections or repairs. It’s also handy for bending and shaping metal before final welding.
5. Spot Welding:
For sculptures incorporating sheet metal or wire elements, spot welding provides quick, localized joins without compromising the overall structure.
Beyond technique selection, sculptors must consider factors like material compatibility, weld durability, and finishing processes (e.g., grinding or polishing) to ensure the sculpture’s longevity and visual appeal. By mastering these methods, artists transform raw metal into breathtaking, enduring art.