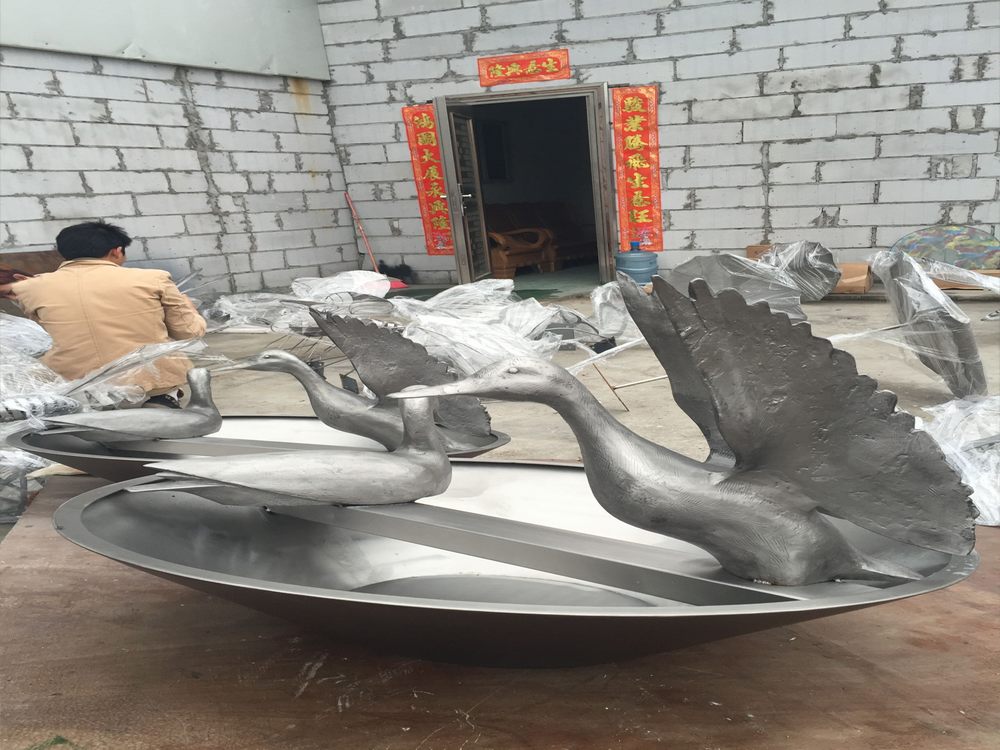
Creating sculptures from dissimilar metals presents unique challenges, but artists and fabricators employ several advanced techniques to achieve seamless and durable joins. One common method is welding, where metals like steel and copper are fused using specialized processes such as TIG or MIG welding, often with filler materials to ensure compatibility. Brazing is another popular choice, especially for metals with differing melting points, as it uses a lower-temperature filler metal to bond components without melting the base materials.
Mechanical fastening, including bolts, rivets, or screws, offers a non-thermal alternative, ideal for sculptures requiring disassembly or adjustable elements. Adhesive bonding with high-strength epoxies is also used for delicate or intricate designs where heat could cause distortion. Additionally, cold joining techniques like crimping or press-fitting provide clean, heat-free solutions for certain metal combinations.
Artists often combine these methods to balance structural integrity with aesthetic appeal, ensuring the sculpture withstands environmental stresses while maintaining its visual harmony. Each technique requires careful consideration of the metals' properties, the sculpture's intended use, and the desired finish, making the process both a technical and artistic endeavor.