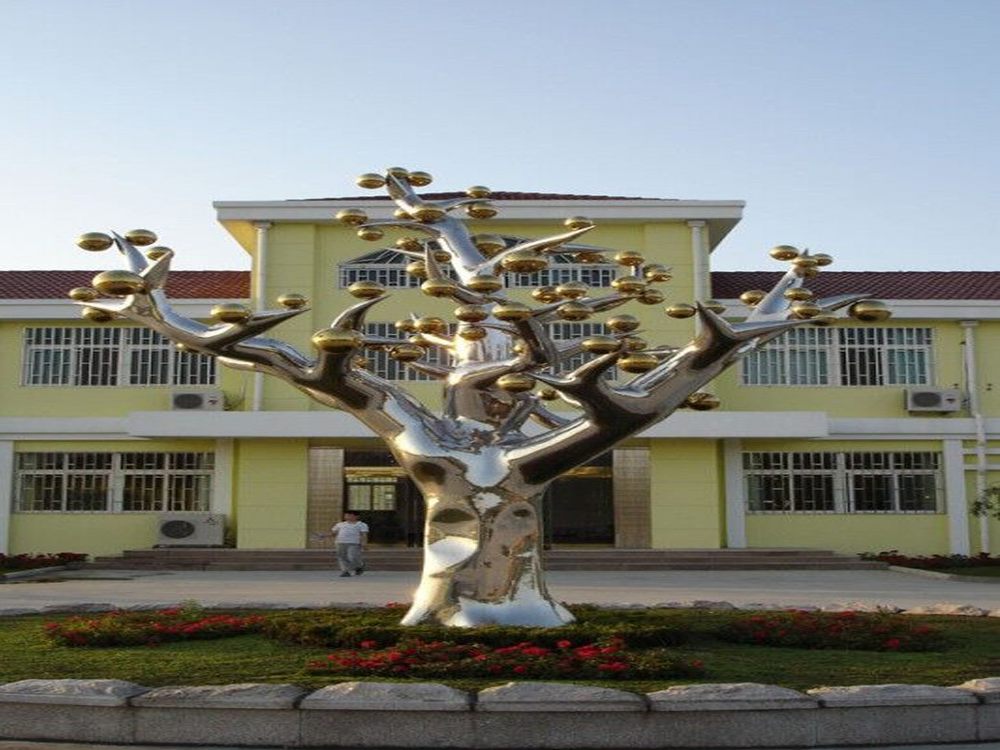
Colorfastness in painted porcelain sculptures is a critical aspect of preserving their beauty and value over time. Artists and manufacturers employ a combination of material science and traditional craftsmanship to ensure vibrant, long-lasting colors.
The process begins with selecting high-quality ceramic pigments that are inherently stable under high temperatures. These pigments are mixed with specialized binders to create paints that adhere firmly to the porcelain surface. The most crucial step is the application of a protective glaze, which serves as a glass-like barrier against environmental factors.
Firing techniques play a pivotal role in achieving colorfastness. Porcelain sculptures undergo precise kiln firing at temperatures between 1200-1400°C, which vitrifies both the clay body and the glaze, creating a permanent bond. Multiple firing cycles may be used for complex pieces, with lower-temperature enamel firings preserving delicate painted details.
Modern manufacturers often incorporate nanotechnology in glazes to enhance UV resistance, while traditional artists might use secret family recipes of mineral-based colors that have proven durable over centuries. Quality control includes accelerated aging tests where pieces are exposed to extreme conditions to simulate years of wear.
The result is porcelain art that maintains its chromatic integrity despite exposure to light, humidity, and handling - a testament to the marriage of artistic vision and technical precision in ceramic arts.