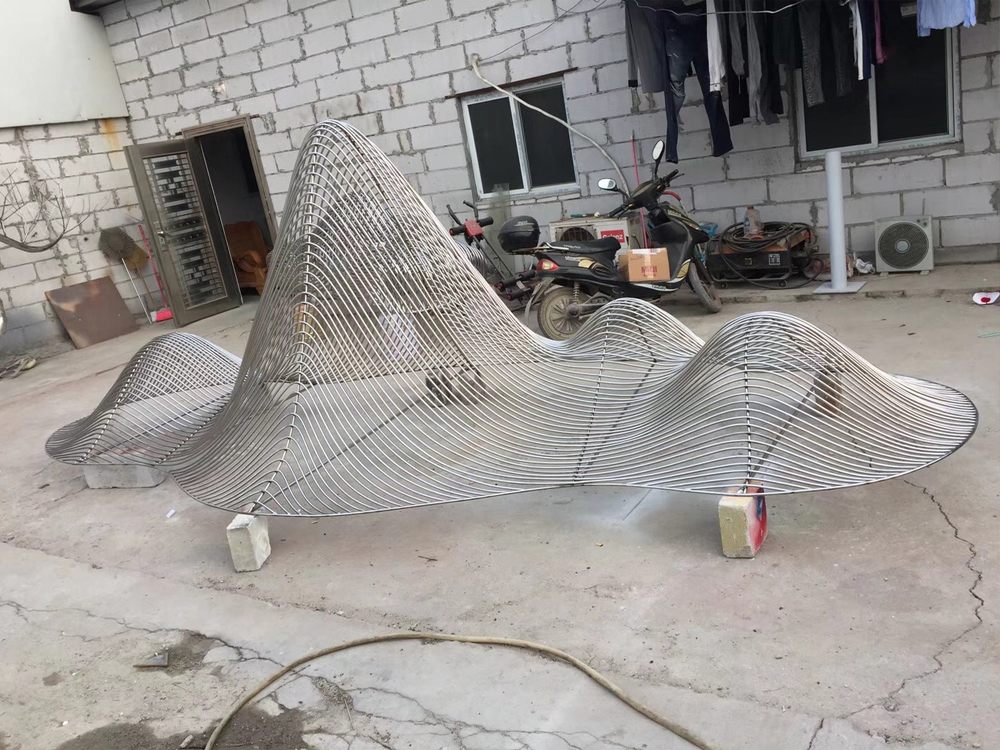
Creating porcelain sculptures with mixed firing techniques presents unique challenges for artists and manufacturers. The process requires a delicate balance of temperature control, material compatibility, and artistic vision.
One major challenge is managing different clay bodies and glazes that react differently under heat. Artists often test small batches to determine optimal firing schedules, ensuring each component matures correctly without cracking or warping. Manufacturers address this by developing specialized kilns with precise temperature zones.
Another hurdle is color consistency. Mixed techniques can cause unpredictable glaze interactions. Solutions include layering glazes strategically or using underglazes for stability. Some artists embrace these variations, turning imperfections into signature styles.
Time management is crucial too. Complex pieces may require multiple firings at varying temperatures. Manufacturers streamline this with computerized kilns, while independent artists often build custom schedules around each piece's needs.
Innovative approaches continue to emerge, like combining electric and gas firing or incorporating raku elements. These hybrid methods push porcelain's boundaries while respecting its centuries-old traditions. Through experimentation and technical mastery, creators transform these challenges into opportunities for breathtaking ceramic art.