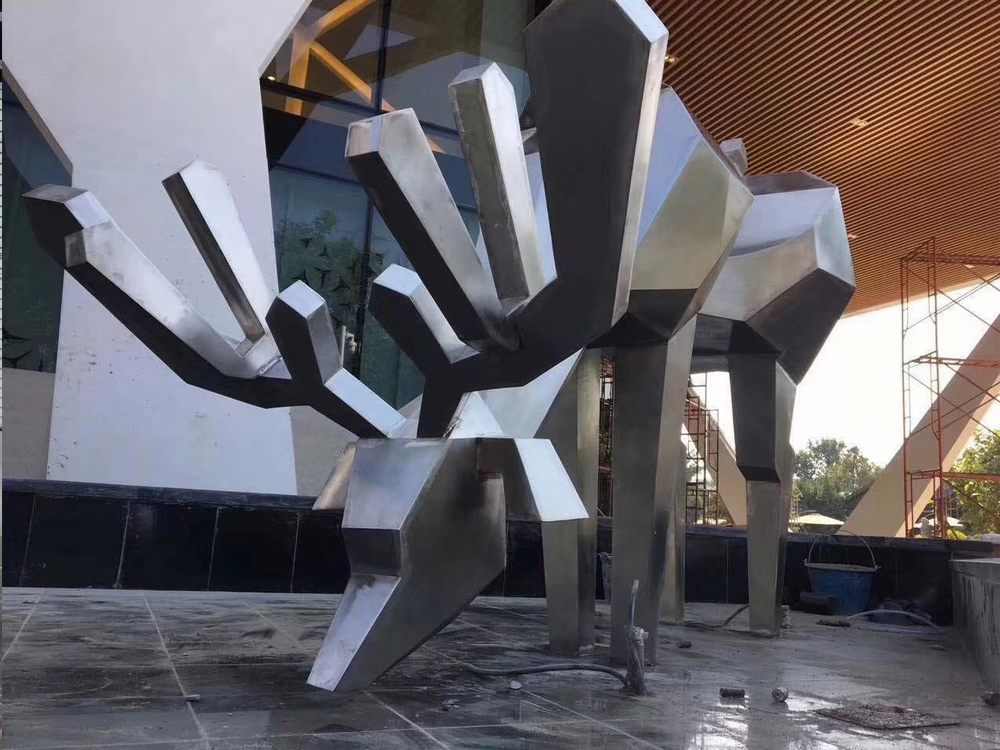
The delicate nature of porcelain makes sculptures particularly vulnerable to defects during creation and firing. Both artists and manufacturers have developed thoughtful approaches to handling these imperfect pieces, balancing artistic integrity with environmental responsibility.
Many ceramic artists repurpose flawed sculptures through creative transformation. Some intentionally break defective works further to create mosaic art or mixed-media installations. Others grind the porcelain into grog - crushed ceramic material reused as aggregate in new clay bodies. This practice not only reduces waste but can add desirable texture and strength to future creations.
Manufacturers often implement systematic recycling programs. Large-scale operations may crush defective pieces for use as drainage material in kiln furniture or as raw material in industrial applications. Some companies have developed closed-loop systems where porcelain waste is reprocessed into new clay after proper refinement.
Environmentally conscious studios are exploring innovative solutions like:
- Partnering with local construction companies to use crushed porcelain as sustainable aggregate
- Creating educational programs where flawed pieces become teaching tools
- Developing special glaze formulas that incorporate porcelain dust
- Offering "seconds sales" where slightly imperfect works are sold at discount
The most sustainable approach begins with prevention. Many artists now use digital prototyping and test firings to minimize defects before committing to final pieces. When flaws do occur, the porcelain art community increasingly views them not as waste, but as opportunities for creative problem-solving and environmental stewardship.
As sustainability becomes paramount in the arts, these responsible disposal and recycling methods demonstrate how traditional ceramic practices can adapt to modern ecological concerns without sacrificing artistic quality.