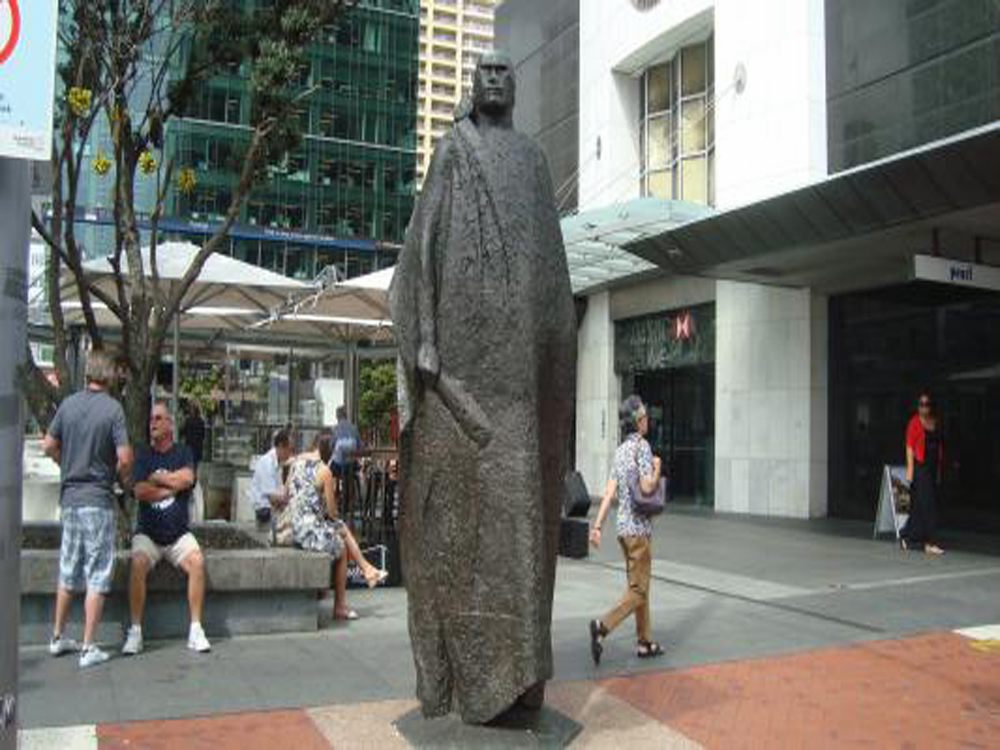
Porcelain sculptures are admired for their delicate beauty, but glaze shrinkage and improper fit can pose significant challenges for artists and manufacturers. These issues often arise due to mismatched thermal expansion rates between the clay body and glaze, leading to cracks, warping, or flaking.
To address this, professionals employ several key strategies. First, they carefully test glaze recipes to ensure compatibility with the clay body. Adjusting the silica, alumina, and flux ratios in the glaze can minimize shrinkage discrepancies. Some artists even create custom blends tailored to their specific clay composition.
Kiln temperature control is another critical factor. Gradual heating and cooling cycles help reduce stress on the material, while precise final firing temperatures ensure optimal glaze maturation without over-shrinking. Many manufacturers use computerized kilns for exact temperature regulation.
For complex sculptures, artists may apply glaze in multiple thin layers rather than one thick coating. This technique allows for better control over shrinkage and reduces the risk of cracking. Some also use specialized underglazes or engobes as intermediary layers to improve adhesion.
Advanced practitioners sometimes employ "dunting" prevention methods, where they design sculptures with uniform thickness to promote even shrinkage. Others incorporate grog (pre-fired clay particles) into their clay bodies to enhance stability during firing.
Contemporary solutions include using digital modeling to predict shrinkage patterns before firing, and some manufacturers now offer pre-shrunk glaze systems specifically formulated for sculptural work. Through these combined approaches, artists continue to push the boundaries of porcelain art while maintaining structural integrity.