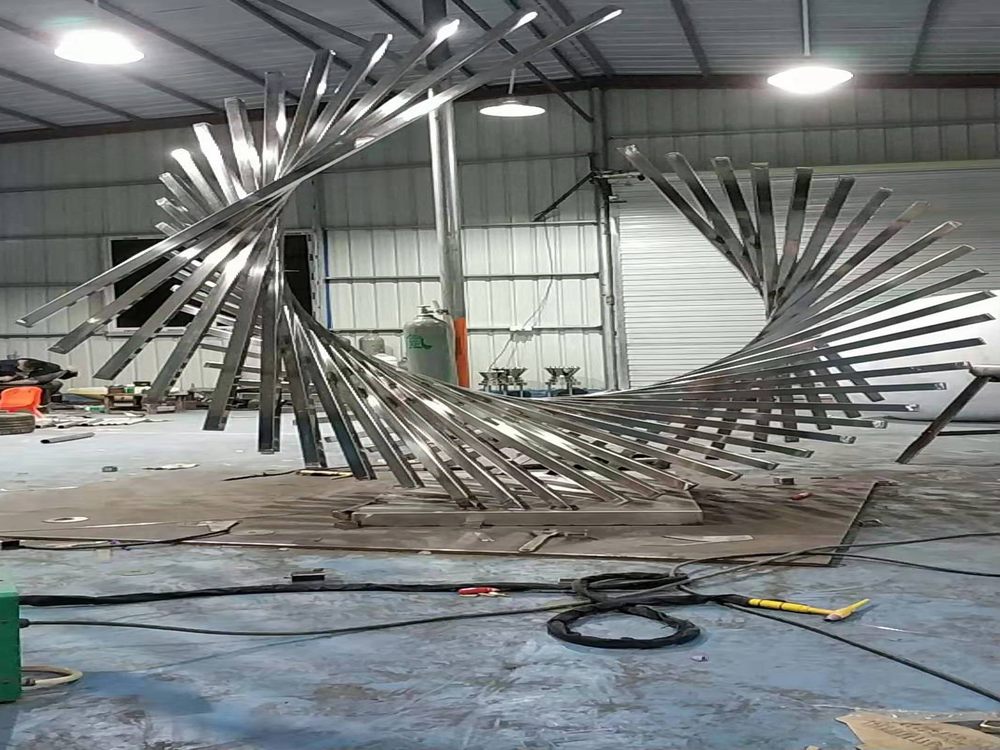
Creating porcelain sculptures with intricate undercuts is a demanding art form that requires both technical precision and creative ingenuity. Artists and manufacturers employ a variety of specialized techniques to address these challenges, ensuring the delicate balance between aesthetic beauty and structural integrity.
One common approach is the use of slip casting, where liquid clay is poured into a mold to capture fine details. For complex undercuts, multi-part molds are often designed, allowing the sculpture to be assembled piece by piece after drying. This method minimizes stress on fragile sections while preserving intricate designs.
Hand-building techniques like coiling and carving are also utilized, particularly for unique or one-of-a-kind pieces. Artists may work in stages, allowing each section to partially dry before adding the next, reducing the risk of collapse. Some even employ supportive armatures or temporary structures during the drying and firing processes.
Modern manufacturers have turned to 3D printing technology to create precise prototypes and molds, enabling the production of undercuts that would be nearly impossible to achieve by hand. This technological advancement has opened new possibilities in porcelain sculpture design.
The firing process presents another critical challenge. Artists carefully control kiln temperatures and heating rates to prevent cracking in areas with undercuts, sometimes using specialized kiln furniture to support delicate sections during firing.
Through these combined methods of traditional craftsmanship and modern innovation, artists continue to push the boundaries of porcelain sculpture, transforming the limitations of undercuts into opportunities for breathtaking artistic expression.