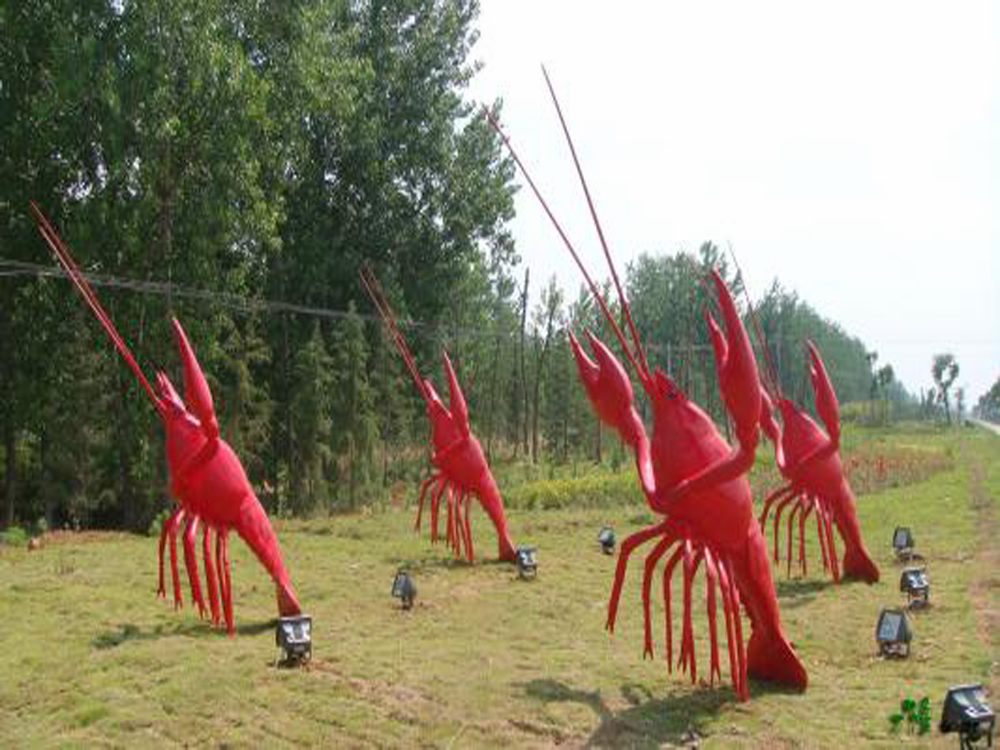
Porcelain sculptures are admired for their delicate beauty, but their production is fraught with potential defects. The most common issues include cracking, warping, glaze imperfections, and color inconsistencies.
Cracking often occurs due to uneven drying or rapid temperature changes in the kiln. To prevent this, artisans carefully control drying times and use kilns with gradual temperature ramping. Warping results from improper clay composition or uneven thickness; this is mitigated through precise mold design and balanced clay mixtures.
Glaze defects like pinholes or crawling happen when application is uneven or firing is incorrect. Solutions include multiple thin glaze layers and controlled firing cycles. Color variations are addressed through standardized pigment mixing and consistent kiln atmospheres.
Modern techniques like computerized kiln controls and 3D-printed molds have significantly reduced these defects. However, skilled artisans remain crucial for quality control, using magnification tools to detect micro-cracks and performing meticulous hand-finishing when needed.
For valuable pieces, professional restoration techniques can repair many defects, though prevention through careful production remains the gold standard in porcelain sculpture craftsmanship.