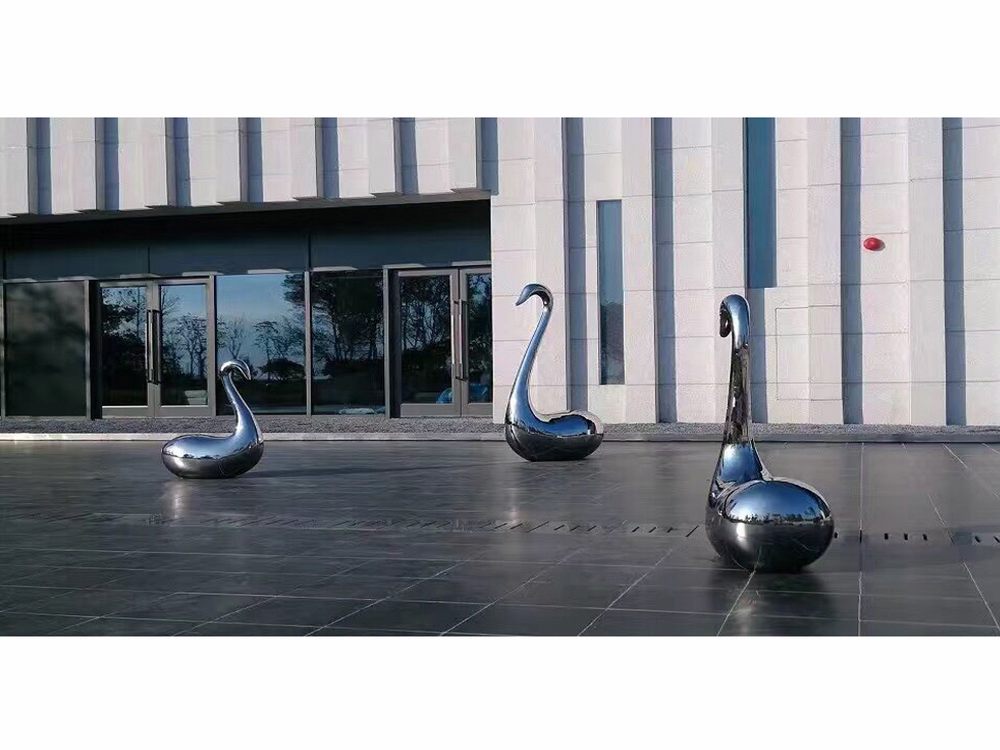
Creating porcelain sculptures with embedded aromatic elements is a delicate fusion of artistry and chemistry, presenting unique challenges for ceramicists. The first major hurdle lies in material compatibility—porcelain's high firing temperatures (often exceeding 1200°C) can destroy most aromatic compounds. Artists must carefully select heat-resistant fragrance carriers or develop post-firing infusion techniques that preserve both the sculpture's integrity and the scent's potency.
Another significant challenge is achieving balanced fragrance dispersion. Unlike porous materials, glazed porcelain surfaces resist scent absorption, requiring innovative solutions like micro-perforations or internal fragrance chambers. The scent's longevity also proves problematic, as encapsulated aromas in non-porous ceramics may fade faster than in traditional diffusers.
Technical precision becomes paramount when incorporating aromatic elements without compromising the sculpture's structural stability. Thin porcelain walls needed for effective scent diffusion increase breakage risks during firing. Additionally, the artistic vision must harmonize with practical constraints—certain fragrances may discolor porcelain or interact unpredictably with glazes.
Modern solutions include using temperature-resistant essential oil blends, nanotechnology encapsulation, or hybrid designs combining porcelain with aromatic wood bases. Despite these challenges, successful aromatic porcelain pieces represent a remarkable marriage of olfactory and visual artistry, pushing the boundaries of ceramic innovation.