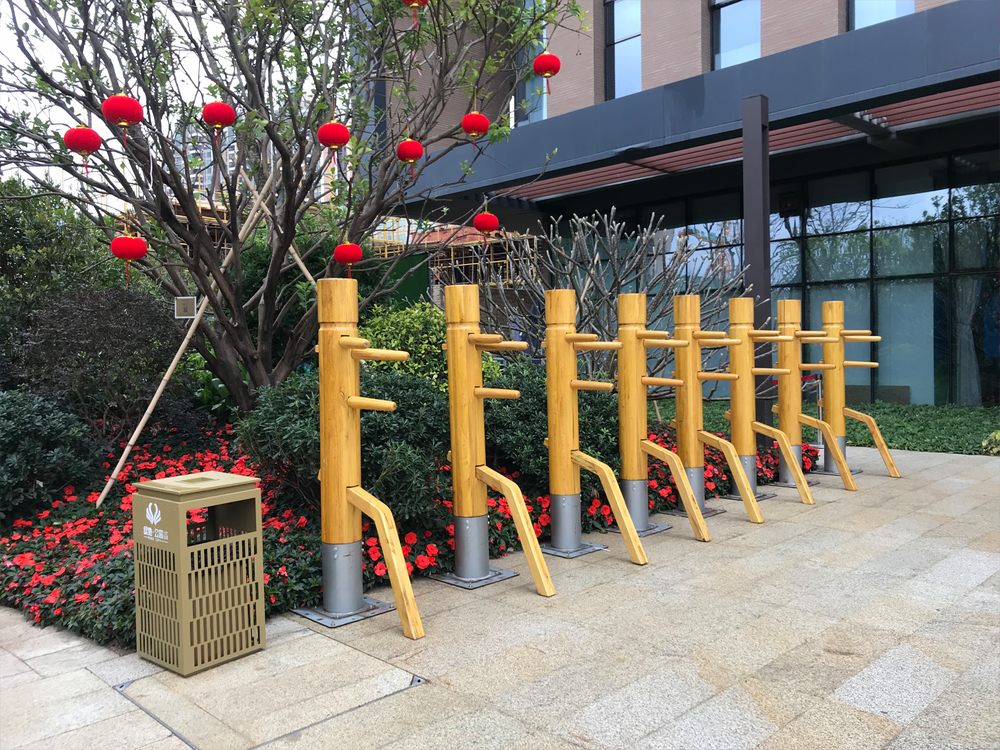
Creating porcelain sculptures with movable or interactive parts is a fascinating yet demanding art form that combines delicate craftsmanship with innovative design. One of the primary challenges is the inherent fragility of porcelain, which makes it susceptible to cracking or breaking during the creation of movable components. Artists must carefully balance the thickness of joints and hinges to ensure durability without compromising aesthetics.
Another significant hurdle is the firing process. Porcelain shrinks during kiln firing, which can misalign or damage movable parts. Precise calculations and multiple test firings are often required to achieve functional results. Additionally, the glazing process adds complexity, as uneven application can hinder movement or fuse parts together.
Designing interactive elements also demands meticulous planning. Artists must consider ergonomics and user interaction while maintaining the sculpture's artistic integrity. The integration of mechanisms like hinges or rotating parts requires advanced technical skills and often collaboration with engineers.
Lastly, the longevity of such sculptures poses a challenge. Repeated movement increases wear and tear on delicate porcelain components, requiring innovative solutions to enhance durability while preserving the artwork's beauty. These challenges make movable porcelain sculptures a true test of an artist's skill and creativity.