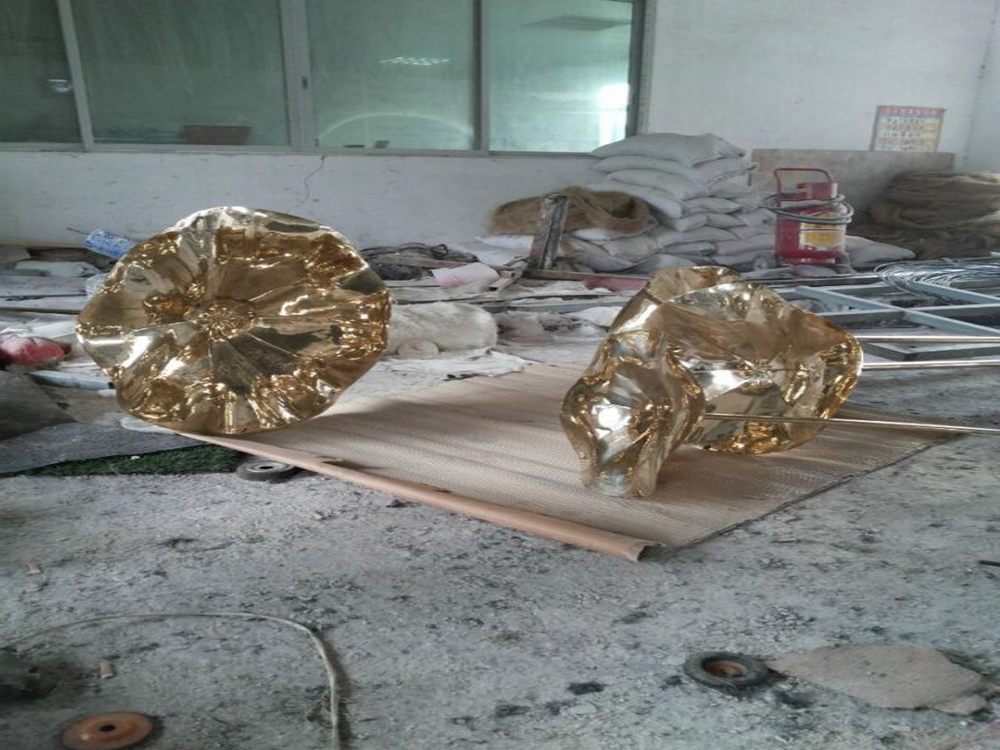
Creating porcelain sculptures with programmable or dynamic surfaces presents a unique set of challenges that blend traditional craftsmanship with cutting-edge technology. One major hurdle is the inherent fragility of porcelain, which complicates the integration of electronic components or mechanisms required for dynamic effects. The material's sensitivity to temperature and moisture also limits the types of programmable elements that can be embedded without compromising structural integrity.
Another challenge lies in achieving seamless interaction between the ceramic surface and dynamic features. Porcelain’s smooth, non-porous texture can hinder adhesion for sensors or responsive coatings, requiring innovative bonding techniques. Additionally, the firing process—a critical step in porcelain production—can damage or destabilize embedded technology, demanding heat-resistant materials and precise kiln control.
Artists and engineers must also navigate the aesthetic balance between functionality and artistry. Programmable surfaces often rely on visible components, which may clash with the delicate, refined appearance of traditional porcelain. Overcoming these obstacles requires interdisciplinary collaboration, pushing the boundaries of both ceramic art and technological innovation.
Ultimately, the fusion of porcelain and dynamic surfaces opens new creative possibilities but demands meticulous problem-solving to harmonize material limitations with artistic vision.