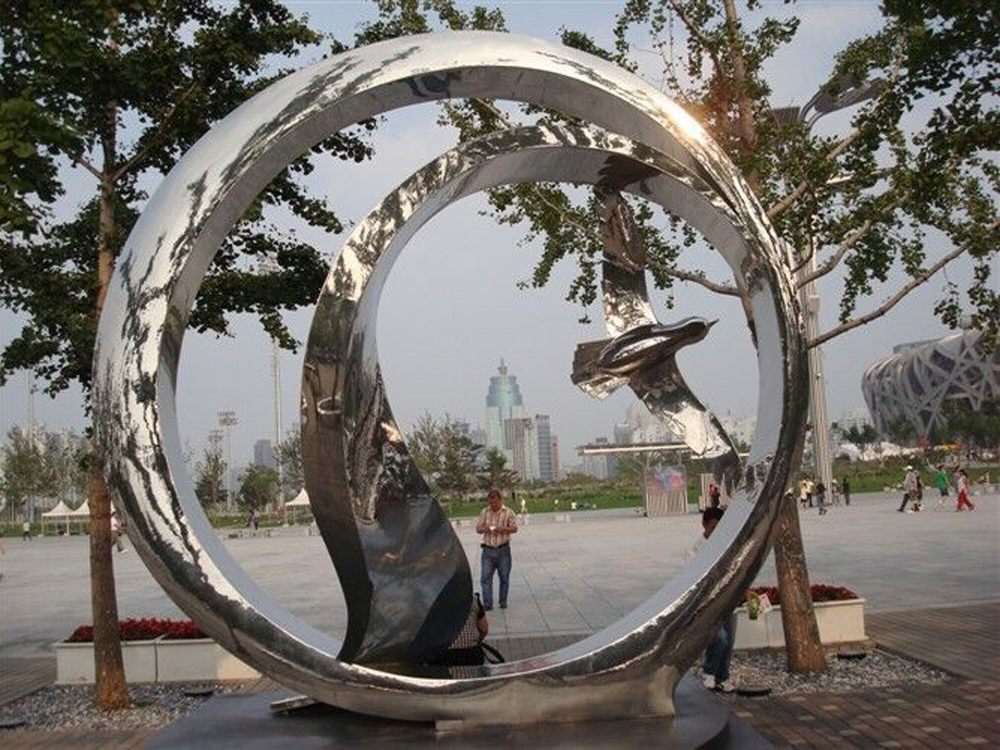
Achieving consistent results with crystalline glazes on porcelain sculptures requires a blend of precise technique, material knowledge, and controlled firing. Here are the best methods to ensure reliability:
1. Glaze Chemistry Mastery: Use high-quality materials with balanced silica, zinc, and flux ratios to promote crystal formation. Test small batches to refine the recipe before full-scale application.
2. Kiln Control: Maintain strict temperature schedules, including a slow cooling phase (around 1100°C) to allow crystals to grow uniformly. Programmable kilns with precise thermocouples are essential.
3. Clay Body Compatibility: Choose porcelain with low impurities and high thermal stability to prevent warping or glaze defects. Pre-fired bisque pieces should be thoroughly cleaned to avoid contamination.
4. Application Consistency: Apply glaze evenly via dipping or spraying, ensuring uniform thickness. Thicker layers (2-3mm) often yield larger crystals but require careful drying to prevent cracking.
5. Firing Atmosphere: Reduce oxidation by limiting airflow during the crystal-growth phase. Some artists introduce slight reduction for unique effects, though this demands experimentation.
6. Documentation: Record every variable—glaze mix, firing curve, and results—to replicate successes and troubleshoot inconsistencies.
By combining these methods, artists can achieve stunning, repeatable crystalline effects on porcelain sculptures, elevating their ceramic artistry.