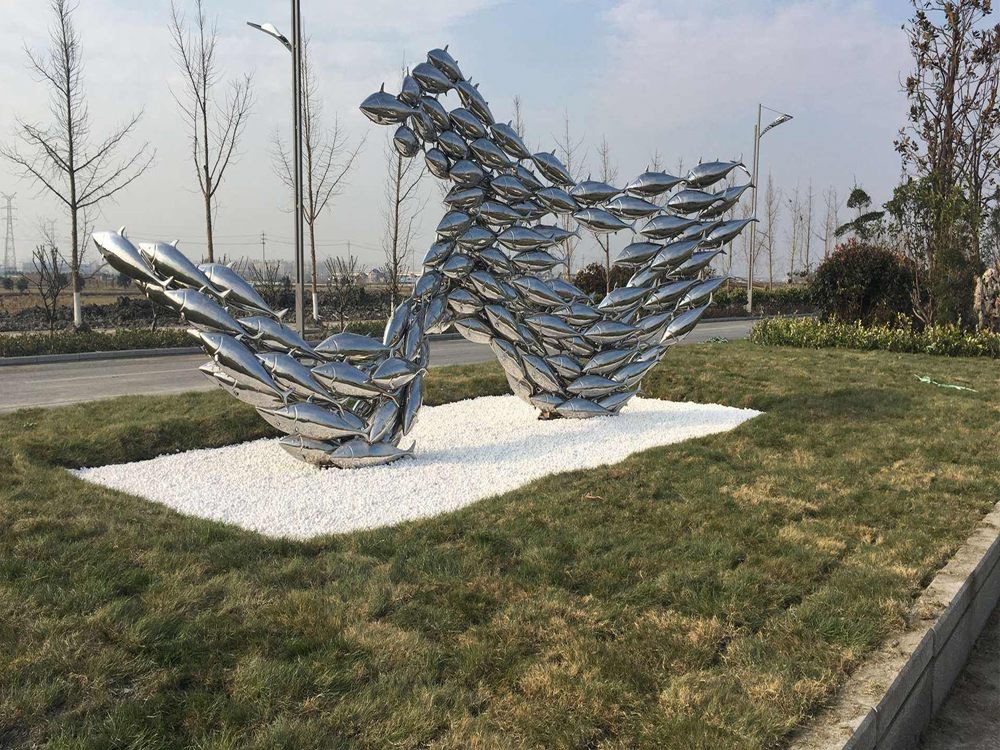
When creating sculptures that incorporate multiple clay bodies, artists face the challenge of ensuring glaze fit—the compatibility between clay and glaze during firing. Different clay types expand and contract at varying rates, which can lead to cracking or glaze defects if not properly managed.
To address this, artists employ several techniques. First, they carefully select clays with similar thermal expansion rates to minimize stress. If dissimilar clays must be used, they may apply intermediary layers or engobes to bridge the differences. Another approach involves testing glaze recipes tailored to each clay body, adjusting fluxes and silica content to achieve a harmonious fit.
Additionally, controlled drying and slow firing cycles are critical. Rapid temperature changes exacerbate fit issues, so artists often use graduated kiln programs to allow even heat distribution. Some even design sculptures with strategic joints or textures to disguise minor fit discrepancies.
Ultimately, mastering glaze fit in mixed-clay sculptures requires a blend of scientific understanding and artistic intuition, ensuring both structural integrity and visual appeal.