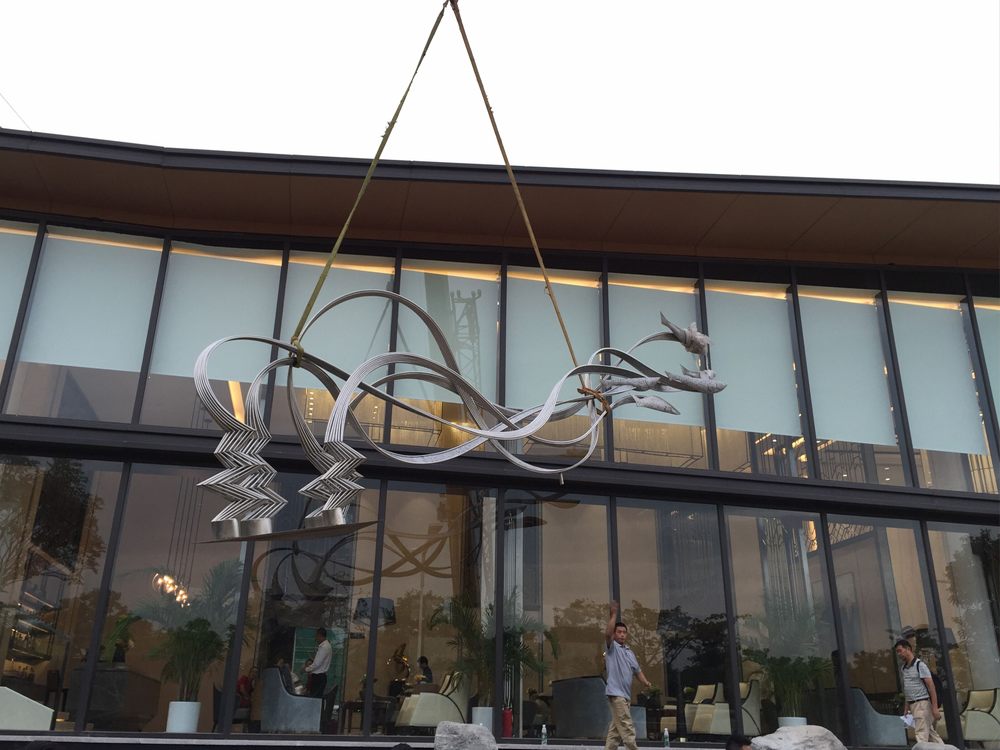
Creating food-safe porcelain sculptures requires meticulous attention to glaze toxicity, a challenge ceramic artists tackle through multiple strategies. First, they select certified non-toxic raw materials, such as lead-free frits and stable metal oxides, which meet FDA or EU safety standards for food contact.
Kiln firing techniques play a crucial role—artists maintain precise temperature controls (typically between 1200°C–1300°C) to fully vitrify glazes, eliminating porous surfaces where harmful chemicals might linger. Many adopt double-firing methods: bisque firing to stabilize the clay body, followed by glaze firing to create an impermeable barrier.
Third-party testing is increasingly common. Studios send finished pieces to laboratories for leaching tests, verifying that no heavy metals (cadmium, lead, etc.) migrate under acidic or alkaline conditions. Some artists even use edible mineral pigments for added safety.
Innovative alternatives like crystalline glazes—formed through controlled cooling cycles—provide vibrant visuals without toxic additives. The community also shares knowledge through guild workshops, emphasizing material SDS (Safety Data Sheets) literacy. Ultimately, combining scientific rigor with artistic skill allows modern ceramists to produce stunning yet safe functional art.