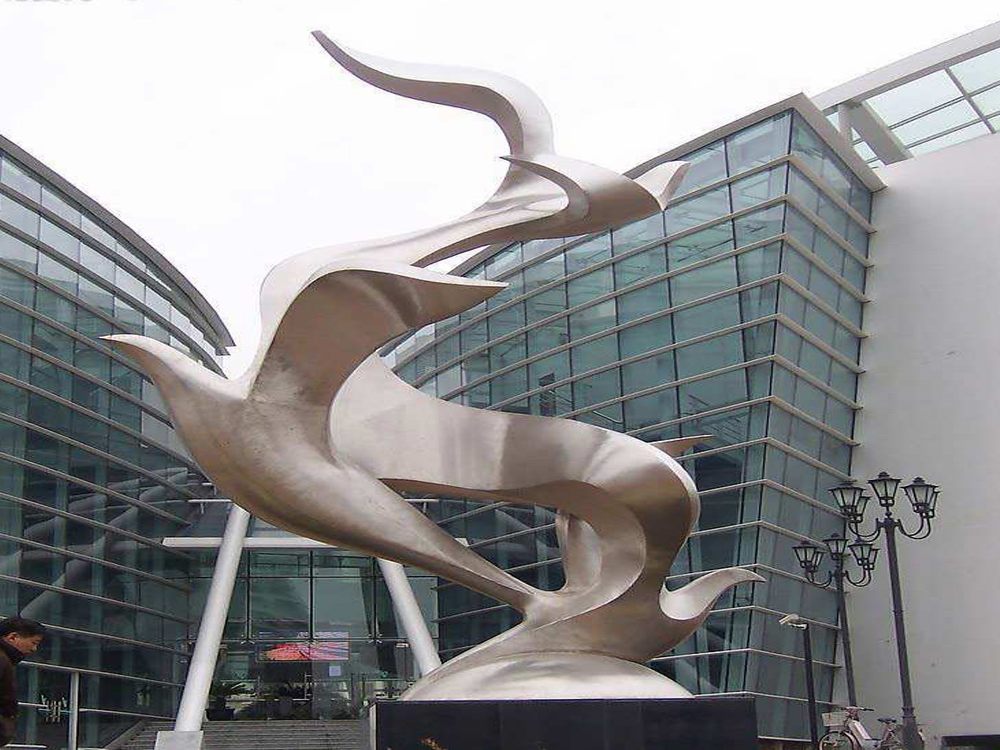
Creating porcelain sculptures with dramatic surface relief presents a fascinating intersection of artistic vision and technical mastery. The primary challenge lies in porcelain's inherent fragility – its low plasticity makes intricate high-relief details prone to cracking during both the forming and drying stages. Artists must carefully balance moisture content, working within narrow time windows before the clay becomes unworkable.
The firing process introduces another layer of complexity. As porcelain shrinks approximately 12-15% during kiln firing, differential shrinkage between thick and thin sections can cause warping or fractures. Particularly problematic are undercut areas and protruding elements, which require specialized support systems during firing. Many sculptors develop custom refractory props or use sacrificial clay supports that vaporize during firing.
Surface tension presents yet another hurdle. Extreme relief creates varying wall thicknesses that dry at different rates, generating internal stresses. Experienced artists employ scoring techniques, controlled drying environments, and sometimes even modify clay bodies with grog or paper fibers to improve structural integrity. The final glaze application must account for how it will flow differently across peaks and valleys of the relief, potentially requiring multiple application methods.
Modern solutions include 3D-printed porcelain prototypes for testing designs, while traditionalists might use plaster molds for particularly challenging sections. Regardless of approach, successful high-relief porcelain sculpture demands both artistic sensitivity and profound material understanding – a testament to why such works command such admiration in the ceramic art world.