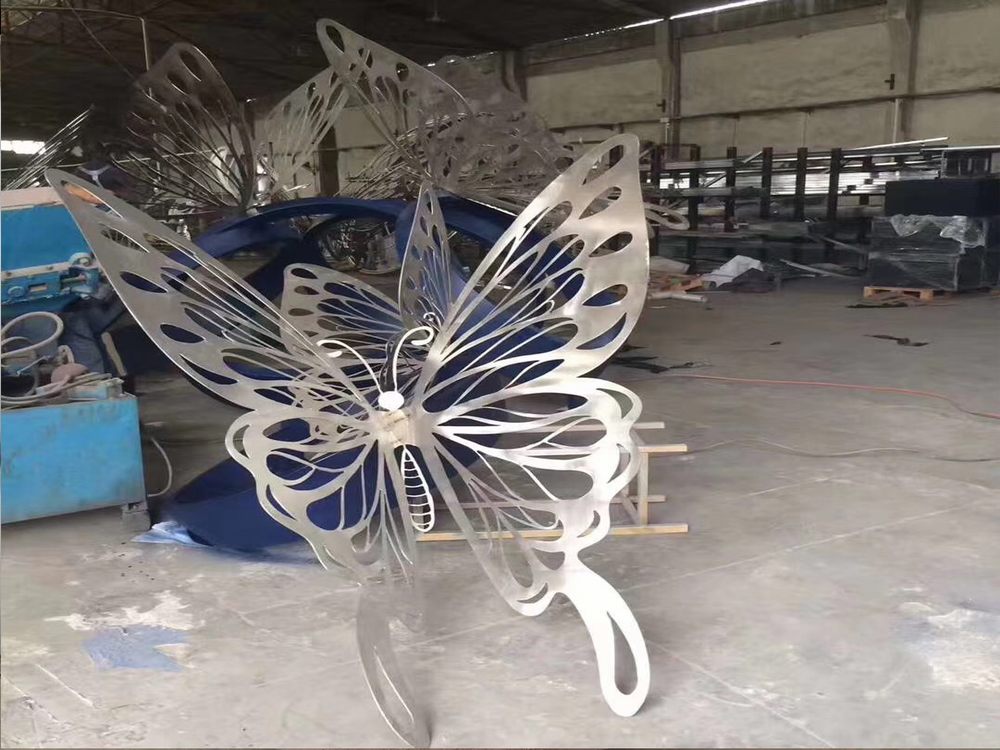
Creating porcelain sculptures with extreme geometric precision presents a unique set of challenges that test the limits of both artistry and technical skill. The very nature of porcelain—a delicate, high-fired ceramic material—makes it particularly difficult to work with when exact angles, sharp edges, and flawless symmetry are required.
One major hurdle is the material's shrinkage rate during firing, which can range from 10-15%. This unpredictable contraction often distorts carefully measured geometries, requiring artists to anticipate and compensate for these changes in their original designs. The high firing temperatures (typically 1200-1400°C) necessary for porcelain also introduce warping risks, especially for thin or extended geometric elements.
Another challenge lies in porcelain's working properties. Unlike more plastic clays, porcelain has limited "memory" when being shaped, making it difficult to maintain crisp edges during hand-building. Even when using molds, the demolding process can damage fragile geometric details.
Contemporary artists address these challenges through innovative techniques like computer-aided design, precision slip-casting, and controlled drying processes. Some combine digital fabrication with traditional ceramic methods to achieve previously impossible geometric forms. However, the fundamental tension between porcelain's organic materiality and geometric perfection continues to make these sculptures some of the most technically demanding works in ceramic art.