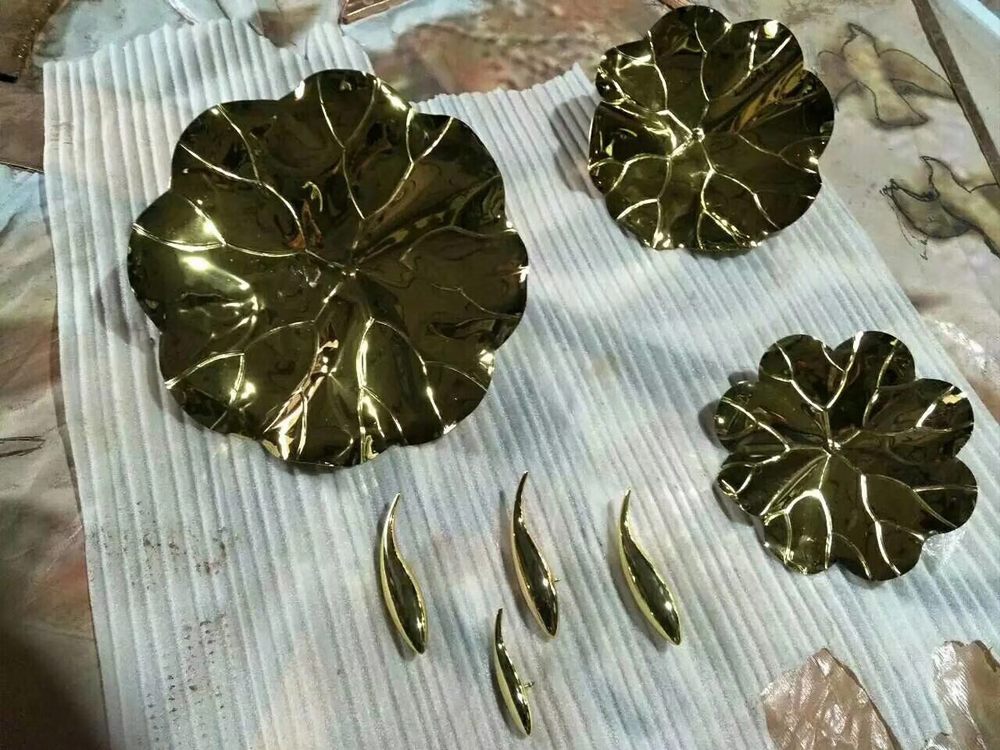
Achieving consistent color matching in glazed porcelain sculptures is a meticulous process that combines artistry, chemistry, and technical precision. Artists begin by selecting high-quality raw materials, including specific mineral-based pigments and clay bodies, to ensure uniformity in composition. The glaze formulation is carefully calibrated, with precise measurements of oxides and fluxes to produce predictable hues after firing.
A critical step involves creating test tiles—small samples fired under controlled conditions—to verify color outcomes before applying glazes to the final sculpture. Kiln temperature and atmosphere are tightly regulated, as even minor fluctuations can alter color results. Electric kilns often provide the most consistent firing environments, while reduction or oxidation atmospheres in gas kilns may introduce intentional variations.
Experienced artists maintain detailed records of glaze recipes, application thickness, and firing schedules. Layering techniques, such as applying translucent glazes over opaque bases, allow for depth and consistency across complex forms. Modern advancements, including computerized kiln controls and spectrophotometer analysis, further enhance precision in color reproduction.
Ultimately, the artist's deep understanding of material behavior and years of hands-on experience remain irreplaceable in achieving the harmonious, repeatable colors that define exceptional glazed porcelain artworks.